Exploring Zoho Inventory's Impact on Manufacturing
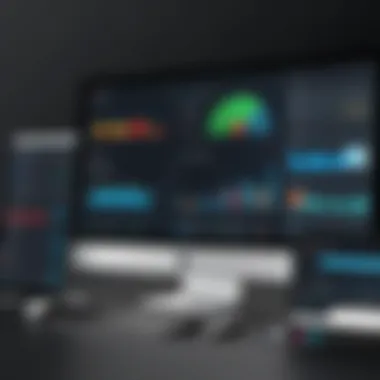
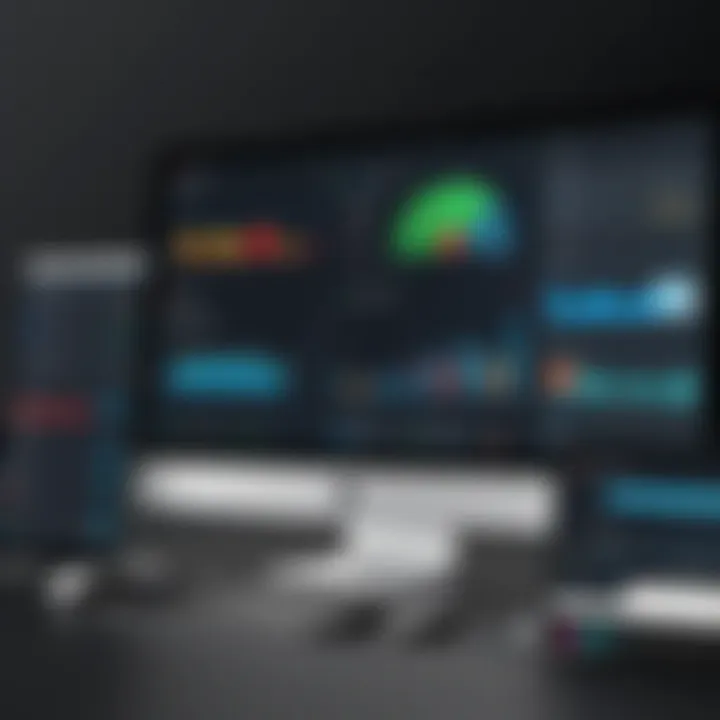
Intro
In the fast-paced world of manufacturing, the efficient management of resources is crucial. As companies strive to optimize their operations, software solutions that streamline processes become invaluable. One such tool is Zoho Inventory, a robust inventory management software that promises to enhance operational efficiencies.
This article will dissect how Zoho Inventory integrates within manufacturing settings. We will explore its various features, analyze the pros and cons, and scrutinize its pricing options. By understanding these facets, professionals will gain insights into the software’s tangible impact on production workflows. Let's dive into the core components of Zoho Inventory and discover how it elevates manufacturing practices.
Software Overview
Features and Functionalities Overview
Zoho Inventory is not just your average inventory management solution; it is tailored for the unique needs of manufacturers. Among its key features is end-to-end inventory tracking. Users can enjoy real-time updates on stock levels, ensuring that they never run out of essential materials.
The software also includes sales order management, making it simple to fulfill orders quickly and accurately. Automated stock alerts notify users when inventory levels fall below a set threshold, thus preventing potential sales losses due to stockouts. Additionally, customizability is a standout feature. Users can create tailored reports that align with their specific business needs.
User Interface and Navigation
When it comes to usability, Zoho Inventory provides an interface that balances aesthetics with functionality. The dashboard is intuitively designed, allowing users to navigate between different sections seamlessly. For instance, finding stock levels or generating reports can be accomplished with just a few clicks.
The presence of helpful drop-down menus and tooltips enhances the user experience. As a result, even those with limited technical skills can efficiently manage their inventory, capturing a broader audience.
Compatibility and Integrations
In today’s interconnected world, compatibility with various systems is essential. Zoho Inventory shines in this regard. It seamlessly integrates with a plethora of other Zoho applications, such as Zoho CRM and Zoho Books, creating a cohesive ecosystem. Additionally, it supports integrations with third-party platforms like Shopify and Amazon, facilitating multi-channel sales.
Pros and Cons
Strengths
One of the standout strengths of Zoho Inventory is its versatility. The software can cater to businesses of varying sizes, from startups to established manufacturing firms. Other advantages include:
- Cost-effective: Competitive pricing compared to similar software.
- User-friendly: Easy onboarding for new users with extensive resources available.
- Comprehensive support: Robust customer service, including live chat and help documentation.
Weaknesses
Despite its many strengths, Zoho Inventory does have drawbacks. Some users have reported limitations when it comes to advanced reporting features. Others have pointed out that complex manufacturing processes may require additional customization effort. It's important for potential users to weigh these considerations against their specific needs.
Comparison with Similar Software
When compared to competitors like TradeGecko and Cin7, Zoho Inventory stands out in terms of pricing and user-friendliness. However, TradeGecko might offer more advanced analytics, while Cin7 boasts stronger point-of-sale integrations. A careful analysis can help businesses determine which software best aligns with their operational requirements.
Pricing and Plans
Subscription Options
Zoho Inventory offers various subscription plans, catering to different business needs. The pricing tiers include:
- Free Plan: Limited features suitable for startups or small operations.
- Basic Plan: A very affordable option ideal for small businesses needing essential features.
- Standard and Professional Plans: Great for larger enterprises requiring expansion capabilities.
Free Trial or Demo Availability
For those who remain skeptical, Zoho Inventory provides a free trial period. This allows potential users to experience the interface and functionalities before committing financially.
Value for Money
Evaluating the cost relative to the features offered, it appears Zoho Inventory provides excellent value. For businesses looking to improve efficiency without breaking the bank, this software presents a compelling option.
Expert Verdict
Final Thoughts and Recommendations
Target Audience Suitability
This software is suitable for small to mid-sized manufacturers, tech-savvy professionals, and IT students who are looking to gain operational insights through practical software applications.
Potential for Future Updates
Given the ever-evolving landscape of technology, one can speculate that Zoho Inventory will continue to develop. Look for enhancements in analytics features and further integrations with emerging platforms in the near future. Keeping an eye on updates will be essential for users wishing to stay at the forefront of manufacturing innovation.
"In the world of manufacturing, staying organized is not just a preference; it's a necessity to thrive."
As we embrace new tools, the importance of informed choices cannot be overstated. Zoho Inventory serves as an invaluable asset for manufacturers aiming to up their game in operational efficiency.

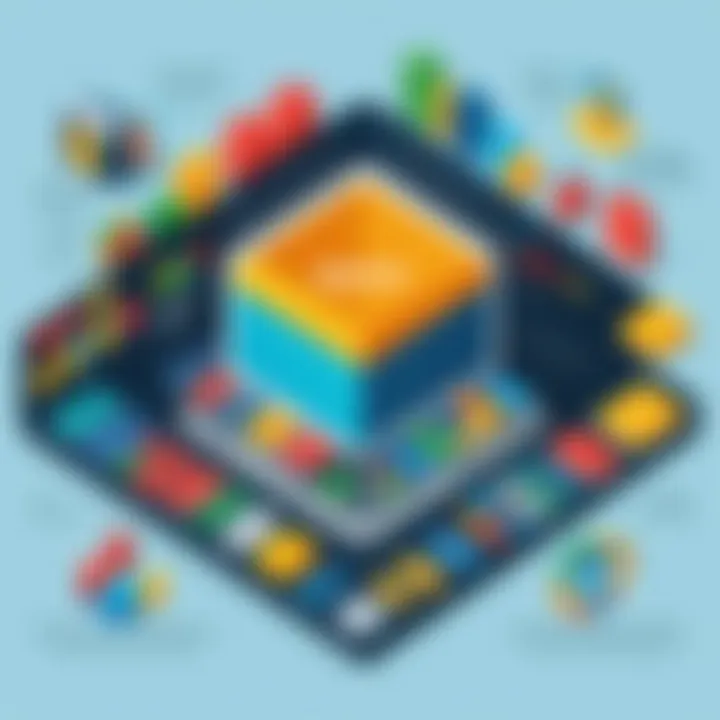
Prelude to Zoho Inventory
In an era where efficiency and adaptability are paramount, Zoho Inventory emerges as a pivotal solution for manufacturers who are looking to streamline their operations. The manufacturing landscape is consistently evolving, constantly presenting challenges and opportunities. It is in this intricate environment that effective inventory management can either break or make a company’s success. By utilizing Zoho Inventory, businesses aim to tackle these challenges head-on.
This section explores the fundamental significance of Zoho Inventory within the manufacturing sector. Its role cannot be underestimated, especially when it comes to optimizing resources and enhancing productivity. A robust inventory management system is crucial for managing stock levels, forecasting demand, and fulfilling orders—operations that are absolutely vital for staying competitive in today's market.
When examining the features of Zoho Inventory, several elements stand out. It not only offers tools for tracking stock but also integrates seamlessly with various other applications within the Zoho ecosystem. This integration facilitates a comprehensive view of operations, enabling manufacturers to make informed decisions quickly. In addition, it can significantly reduce errors in order processing and inventory control—two areas where even small mistakes can lead to considerable setbacks.
One key benefit of deploying Zoho Inventory is its ability to consolidate data. Instead of juggling multiple software systems, manufacturers can harness a single platform that wraps everything from order fulfillment to stock monitoring into one coherent package. This not only improves productivity but also enhances team collaboration, as all stakeholders can access the same real-time information.
Moreover, the considerations surrounding the implementation of Zoho Inventory encompass both technical aspects and staff readiness. As with any software deployment, there may be a learning curve. Therefore, investing time in training and familiarizing staff with the platform is critical for maximizing its benefits.
Ultimately, understanding Zoho Inventory's capabilities and advantages is essential for any manufacturer aiming to refine their supply chain and boost overall efficiency. Its importance lies not just in managing stock but in transforming how businesses operate in a highly competitive realm.
"Technology is best when it brings people together."
In summary, as manufacturers delve into the specifics of Zoho Inventory, they will find that it provides the necessary tools to navigate the complexities of inventory management. The road ahead is not without challenges, but with the right strategy and resources, success is well within reach.
The Role of Inventory Management in Manufacturing
In the realm of manufacturing, inventory management serves as the backbone of production processes. It is more than just keeping count of goods; it involves strategically controlling and overseeing the ordering, storing, and use of components that a company needs to manage its operations efficiently. Without a robust inventory management system, manufacturers can find themselves in a quagmire of lost sales, excess inventory, or stockouts, all of which can be detrimental to the bottom line.
Importance of Inventory Management
Firstly, effective inventory management helps in optimizing production efficiency. By maintaining the right level of stock, manufacturers can ensure that they have sufficient materials on hand to meet production demands. This reduces the risks of halting production due to shortages. A production halt, even for a short period, can ripple through a supply chain, causing delays and compounding costs.
Secondly, inventory management directly influences cash flow. Holding too much inventory ties up critical cash that could be used for other operational needs. Conversely, having too little can result in missed opportunities and dissatisfaction from customers if orders cannot be fulfilled on time. Striking a balance is where sophisticated inventory management tools, like Zoho Inventory, come into play.
Benefits of Efficient Inventory Control
Among the myriad of benefits, one cannot overlook the enhancement of customer satisfaction. When inventory levels are properly managed, it leads to reliable delivery times and the ability to meet customer demand effectively. Happy customers are likely to return, which proves beneficial in the long term for manufacturers.
Additionally, managing inventory with precision contributes to cost reduction. Efficient systems prevent overstocking items that can become obsolete. In a rapidly changing market, agility in inventory management allows businesses to adapt to consumer trends without incurring excess costs.
Considerations in Inventory Management
Regardless of the size of the business, managers must contend with various challenges when it comes to inventory. For instance, demand forecasting plays a vital role. Predicting how much product to manufacture, based on past trends and market analysis, can be daunting. Incorrect forecasts can lead to either too much stock or too little, both scenarios having unwanted repercussions on both finances and operations.
Understanding the complexities of supply chain logistics is another consideration. From sourcing raw materials to distributing finished goods, each step can impact inventory levels significantly. A hiccup in any area can lead to inventory discrepancies that require troubleshooting and can cause domino effects across multiple departments.
"Effective inventory management acts as a compass, guiding manufacturing firms to navigate the intricate waters of supply and demand."
In summary, the role of inventory management in manufacturing cannot be overstated. It encompasses a broad spectrum of tasks that sustain production, optimize cash flow, enhance customer satisfaction, and streamline operations. As we delve deeper into Zoho Inventory in subsequent sections, the significance of these management practices will become even more evident, exemplifying how they collectively contribute to an organization’s overall success.
Key Features of Zoho Inventory
Zoho Inventory is not just another tool in the vast sea of inventory management software; it stands out due to its array of features tailored specifically for the manufacturing sector. Understanding these features is crucial, as they directly contribute to a smoother operational flow, improve accuracy, and ultimately drive profitability. The importance of these key functionalities lies in their ability to transform complex inventory tasks into manageable processes, making life easier for manufacturers who face the constant pressure of managing resources efficiently.
Inventory Control
In manufacturing, keeping track of every single item is akin to walking a tightrope. Zoho Inventory's Inventory Control feature takes the guesswork out of stock management. It allows for real-time tracking of inventory levels, which can drastically reduce the instances of overstocking or stockouts.
Imagine a scenario where a manufacturer of electronic components uses Zoho Inventory. Each component, no matter how small, can be monitored precisely. Whenever a component dips below a predefined threshold, alerts can trigger, ensuring timely replenishments. This proactive approach not only ensures that production lines do not stall but also boosts customer satisfaction by meeting delivery timelines without delay.
Moreover, this feature supports batch and serial number tracking. This is a game changer in sectors where traceability is not just recommended but mandated by regulations, such as pharmaceuticals or food production. The immediate access to historical stock data allows businesses to conduct thorough audits, should the need arise, thus strengthening compliance postures.
Order Management
The heart of any manufacturing process often lies in its order management system. With Zoho Inventory's Order Management capabilities, manufacturers can streamline the entire order fulfillment process from start to finish. This starts from the moment an order is placed, carrying through to shipping and delivery.
For instance, consider a textile manufacturer that receives an order for a custom batch of clothes. Using Zoho Inventory, the order can be tracked at every step – from raw material sourcing to the final shipping. The integrated platform enables multiple sales channels, which allows manufacturers to aggregate orders coming from different sources, greatly enhancing efficiency.
Ordering can be automated, reducing manual errors and speeding up response times. Customers can be notified of order statuses automatically, ensuring transparency in the process.
Furthermore, the software allows for the management of backorders. When demand is high and stock runs low, this feature enables organizations to take pre-orders while they restock, keeping clients engaged and satisfied even when delays occur.
Integration Capabilities
Zoho Inventory's Integration Capabilities are perhaps one of its most intriguing features. In an age where different software systems need to coexist seamlessly, the ability to integrate with various platforms is a massive advantage.
Zoho Inventory plays well with other software solutions, including Zoho Books for accounting and Zoho CRM for customer management. This interconnectivity means that all departments can work from a unified data set. When an order is placed, for example, the accounting team instantly sees that sale reflected in Zoho Books, allowing them to update the financial records without additional manual data entry.
Furthermore, integrations with various e-commerce platforms like Shopify and Amazon mean that the inventory can be managed across different sales channels without any fuss. When stock levels change in Zoho Inventory after a sale, this data syncs across platforms, preventing overselling and enhancing customer experience.
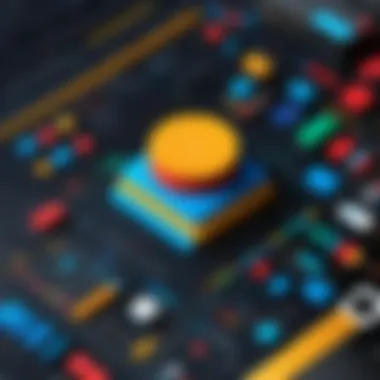
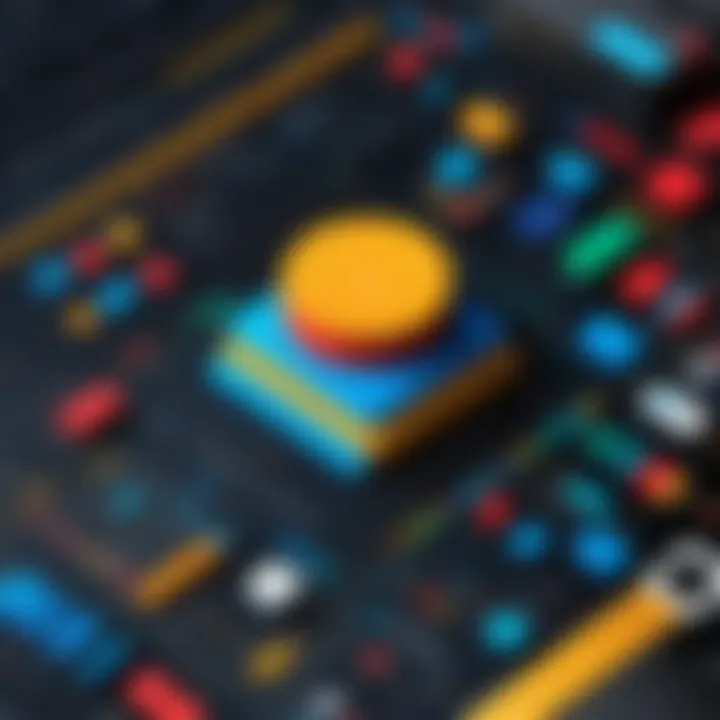
These integration capabilities lead to a holistic management approach, vastly improving operational efficiency and enabling manufacturers to adapt swiftly to market changes. As the manufacturing landscape continues to evolve, the importance of such features cannot be overstated.
"Managing inventory effectively is the backbone of operational excellence in any manufacturing setup."
Benefits of Using Zoho Inventory in Manufacturing
Leveraging Zoho Inventory in manufacturing offers significant advantages that can transform operational dynamics. Efficiency, cost-effectiveness, and accuracy stand out as core areas where the platform makes a substantial impact. By drawing on these benefits, manufacturers can navigate their day-to-day challenges and adapt to fast-paced industry changes. In this section, we explore these specific elements in depth, highlighting how they contribute to smoother workflows and better decision-making.
Increased Efficiency
One of the most compelling reasons for adopting Zoho Inventory revolves around its ability to streamline processes. Manufacturers often grapple with myriad tasks—tracking stock, managing orders, and fulfilling production requirements can turn into a logistical nightmare without a robust system. With Zoho Inventory, users experience a significent reduction in time spent on these activities. The software facilitates:
- Automated Replenishment: Notifications for low stock levels eliminate guesswork, enabling timely restocking.
- Real-time Inventory Tracking: Live updates provide insights into product status, allowing teams to make informed decisions.
- Optimized Order Processing: Orders can be managed and tracked through a single interface, reducing errors and enhancing overall productivity.
This integration decreases lead times and elevates productivity, ultimately helping companies meet consumer demands more effectively.
Cost Reduction
Manufacturers always seek ways to trim operational costs. With Zoho Inventory, significant savings can be achieved through a variety of features:
- Minimized Overheads: Automation reduces the need for excessive manpower focused on manual tracking, thus lowering labor costs.
- Inventory Optimization: The platform's analytics tools identify slow-moving products, which prevents unnecessary overstocking and frees up cash flow.
- Reduced Waste: Precise inventory management curtails spoilage or obsolescence, especially for manufacturers dealing with perishable goods. Minimizing excess means decreasing throwaway costs, leading to a healthier bottom line.
By effectively managing resources, manufacturers observe not only direct natural savings but also an overall more sustainable operational model.
Enhanced Accuracy
In manufacturing, precision is paramount. Errors in inventory management can snowball into production delays or financial losses. Zoho Inventory enhances accuracy significantly, which can be attributed to:
- Data Integrity: Automated inputs and updates minimize manual entry mistakes, providing reliable data for decision-making.
- Barcode Scanning: Incorporating barcode scanning technology enables quick verification, ensuring that the right items are tracked and used in production.
- Reporting and Analytics: Ad-hoc reports generated help identify discrepancies swiftly, allowing for corrective actions before issues escalate.
By prioritizing accuracy, manufacturers not only safeguard their reputation but also enhance trust among stakeholders, paving the way for long-term growth.
In summary, the integration of Zoho Inventory within the manufacturing sector presents noteworthy benefits. Increased efficiency, notable cost reductions, and heightened accuracy facilitate smarter operations, allowing manufacturers to navigate their unique challenges adeptly.
Challenges in Inventory Management for Manufacturers
In the ever-evolving landscape of manufacturing, effective inventory management presents a myriad of challenges. The balance between demand and supply is like walking a tightrope; one misstep can lead to cascading effects down the supply chain. Understanding these challenges is paramount for manufacturers aiming to sustain their competitive edge and streamline their operations.
Inventory management is all about maintaining the right stock levels to meet customer needs without overcommitting resources. One of the most pressing issues is managing stock levels effectively. This involves not only keeping track of materials and parts but also ensuring that production processes remain uninterrupted. Manufacturers often struggle with excess stock, which can lead to increased holding costs, and conversely, stockouts that may halt production. The financial implications of these mismanagements can be significant, impacting cash flow and overall profitability.
Furthermore, forecasting demand accurately is another critical hurdle. Market dynamics can shift rapidly due to various factors, like changes in consumer preferences, economic downturns, or even global events. Manufacturers need to predict these changes to adjust their inventory levels accordingly. Failure to do so could result in overproduction or underproduction, which further complicates inventory issues. Keeping abreast of market trends, sales data, and consumer behaviors is essential, yet many manufacturers find this a daunting task.
Both of these challenges leave manufacturers at a crossroads and must be addressed head-on. By leveraging inventory management software like Zoho Inventory, companies can mitigate risks associated with managing stock levels and forecasting demand. Automated alerts, analytics, and integration capabilities provided by such software can ease the burden and ensure a smoother operational flow.
"Effective inventory management is not just about having stock; it's about having the right stock at the right time."
To successfully navigate the labyrinth of inventory management, manufacturers must consider employing advanced strategies that fit their unique needs. Below, we delve into the details of managing stock levels and forecasting demand, both significant components in the inventory management puzzle.
Managing Stock Levels
Managing stock levels is akin to conducting a symphony; every section must play in harmony to achieve the desired result. For manufacturers, this means having enough inventory to meet production needs without overstuffing their warehouses. The golden rule here is to adopt a just-in-time (JIT) approach, ensuring materials arrive only as they are needed.
Key Strategies for Managing Stock Levels:
- Real-Time Tracking: Implement systems that allow for real-time inventory tracking. This can provide immediate insights into stock levels and trigger re-order notifications when levels dip to a pre-set threshold.
- Cycle Counting: Regular cycle counts can help identify discrepancies between physical stock and records, ensuring accuracy and reducing the risk of stockouts.
- Utilizing Forecasts: Combining sales forecasts with inventory data can guide manufacturers in adjusting their stock levels ahead of demand surges, thus avoiding overages and shortages.
Forecasting Demand
Forecasting demand is inherently challenging; it requires a keen understanding of various market influences. Manufacturers must move beyond intuition, relying on data analytics and historical trends to predict future needs accurately.
Important Considerations in Demand Forecasting:
- Data Analysis: Analyzing past sales data for trends can provide valuable insights into seasonal fluctuations and consumer behavior patterns.
- Market Research: Staying informed on market trends and competitor activities can aid in anticipating changes in demand that may impact inventory needs.
- Flexible Modeling: Employing flexible forecasting models allows for adjustments based on real-time data inputs and unexpected market shifts.
Real-World Applications of Zoho Inventory
When it comes to real-world applications of Zoho Inventory, we cross the boundary from theoretical capability to practical implementation. Understanding how this tool fits within the manufacturing realm can make or break a company’s operational efficiency. This section digs deep into various case studies that highlight the versatility of Zoho Inventory, showcasing how both small manufacturers and large production facilities leverage its functionality to meet their unique needs.
Companies these days operate in an environment where agility and precision are crucial. Real-time inventory tracking and easy integration with financial and customer relational tools leads to better decision-making. It’s also essential to recognize that each business has challenges that require tailored solutions. The essence of Zoho Inventory is not merely what it offers but how it delivers value through case-driven outcomes.
Case Study: Small Manufacturer
Let’s take a look at a small manufacturer, let’s say a custom furniture shop named WoodWorks. WoodWorks specializes in bespoke items, which means their inventory is always changing based on client orders and design selections. Prior to adopting Zoho Inventory, the owner spent countless hours managing orders on spreadsheets, often leading to overstock and occasionally missing urgent client requests.
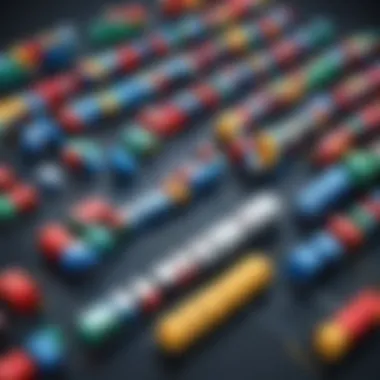
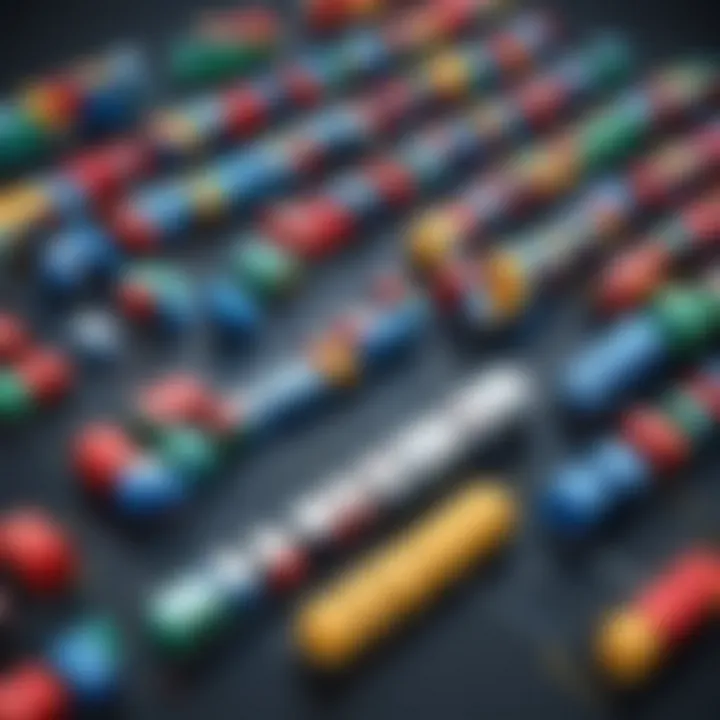
Once they implemented Zoho Inventory, immediate effects were apparent:
- Accurate Stock Levels: With automated stock level updates, they no longer scrambled to find materials just before a deadline.
- Simplified Order Management: Now having a centralized dashboard allows the team to track orders from inception to delivery with a few clicks.
- Integration with Zoho Books: This connection provided an effortless flow between inventory levels and accounting, eliminating guesswork when invoicing clients.
The transformation was striking, leading to a 20% reduction in turnaround time and improved customer satisfaction. WoodWorks thrived, showcasing how a small manufacturer can harness the power of software to eliminate inefficiencies and elevate service delivery.
Case Study: Large Production Facility
Consider a larger facility, like ABC Manufacturing, which specializes in mass-produced electronic components. With different production lines and a vast array of inventory types—some components in high volume and others specialty items—inventory management became a daunting task. Before Zoho Inventory, coordination between various departments was a challenge which often led to production delays and stock discrepancies.
Their experience with Zoho Inventory showcased how technology can scale operations:
- Multi-location Management: ABC Manufacturing has multiple warehouses across the country. Zoho allowed them to track inventory across all locations in real-time.
- Demand Forecasting: By utilizing analytics features, they could predict upcoming stock needs better, reducing excess inventory costs.
- Integration with Zoho CRM: Customer data from Zoho CRM enabled them to prioritize orders effectively based on client demand and historical trends.
Post-implementation, ABC Manufacturing saw a 15% increase in operational efficiency. Workflow became more streamlined, and teams reported higher morale since they were no longer bogged down by manual processes. It’s an excellent testament to how custom solutions can lead to greater productivity.
"The best way to predict the future is to create it." - Peter Drucker
Ultimately, real-world applications of Zoho Inventory unveil its transformative capacity in diverse manufacturing settings.sThis could not only lead to increased efficiency but also foster innovation in operation practices. Overall, companies can adopt a more robust, agile approach to inventory management, reflecting the current demanding landscape of manufacturing.
Integrating Zoho Inventory with Other Zoho Products
Integrating Zoho Inventory with other Zoho products is quite pivotal for manufacturers looking to streamline their overall processes. This integration extends beyond mere data sharing; it fosters a synergy among different functionalities that can significantly elevate operational efficiency.
When different software systems can communicate seamlessly, businesses benefit from reduced manual data entry, fewer errors, and more accurate reporting. In a context where every minute counts, the integration becomes a valuable asset. It allows manufacturers to maintain constant oversight of their operations, aligning inventory management with financial tracking and customer relationship management.
Zoho Books
Zoho Books stands out as an essential tool that works in tandem with Zoho Inventory. It provides manufacturers with a comprehensive accounting solution, allowing them to keep their financials organized. Here are a few of the key benefits this integration brings:
- Real-time Financial Insights: By integrating with Zoho Inventory, Zoho Books ensures that inventory changes reflect immediately in financial reports. This gives manufacturers a clearer view of their profitability and cash flow.
- Simplified Invoicing: Automated invoicing minimizes the chances of human error and ensures timely payments. When an order is fulfilled in Zoho Inventory, the invoice is generated in Zoho Books automatically, streamlining accounting processes.
- Expense Management: The integration allows tracking of inventory-related expenses more effectively. This feature provides a fuller picture of where money is flowing in and out of the business, facilitating better decision-making.
For example, a mid-sized furniture manufacturer that uses Zoho Inventory for tracking the components of their products and Zoho Books for handling their finances may experience a drastic reduction in month-end reconciliation time. Instead of sorting through piles of unsorted data, they can enjoy organized, real-time figures that are easily accessible.
Zoho CRM
Another vital integration for manufacturers is with Zoho CRM. The combination of Zoho Inventory and Zoho CRM can create a more nuanced understanding of customer demands and stock availability. Here’s how that looks in practice:
- Enhanced Customer Experience: By having access to inventory levels through CRM, sales teams can provide customers with accurate information about product availability. It eliminates the back-and-forth that usually happens, leading to quicker response times.
- Forecasting Sales Trends: Integrating these two platforms allows manufacturers to analyze historical sales data alongside current inventory levels. This effectively aids in demand forecasting, which is crucial for minimizing stockouts or overstock situations.
- Order Tracking: Once an order is placed in Zoho CRM, it can be connected to Zoho Inventory, ensuring that the status is visible to both sales staff and customers. This fluidity helps in managing expectations and enhances trust in the brand.
The Future of Inventory Management in Manufacturing
The landscape of inventory management in manufacturing is evolving at a rapid pace. It is crucial to understand where this field is heading to adapt and thrive in the competitive environment. As industries face increasing demands for efficiency and accuracy, the integration of advanced technologies and innovative software solutions will be pivotal. With Zoho Inventory at the forefront, manufacturers can streamline processes, reduce costs, and enhance productivity in ways that were unimaginable a decade ago.
Emerging Technologies
One of the most significant factors shaping the future of inventory management is the rise of emerging technologies. Technologies like Artificial Intelligence (AI), Machine Learning, and the Internet of Things (IoT) are becoming increasingly integrated into inventory practices. These innovations offer real-time data analytics, which can assist in inventory forecasting and help optimize stock levels.
- AI and Machine Learning: These technologies can analyze historical data and trends to predict future inventory needs. This can minimize stockouts and excess inventory, which can tie up resources and affect production timelines.
- IoT Devices: By embedding sensors in storage and transport equipment, manufacturers can achieve real-time monitoring of inventory items. This connectivity allows for a more responsive approach to inventory management. For instance, a manufacturer can immediately detect a drop in stock levels and work proactively to restock before hitting critical levels.
The synthesis of these technologies not only augments operational efficiency but also improves decision-making processes, ensuring that informed strategies are employed to meet production demands.
Trends in Software Development
Not only are the technologies evolving, but the software that manufacturers rely on is also experiencing a transformation. Modern software solutions are moving towards greater adaptability and user-friendliness. The following trends are noteworthy:
- Cloud-Based Solutions: Many manufacturers are shifting toward cloud-based inventory management systems. This transition not only provides accessibility from anywhere but also allows for real-time updates, fostering collaboration across departments.
- Mobile Integration: With the rise of mobile devices, software solutions are being designed with mobile access in mind. This enables managers to track inventory, manage orders, and respond to issues on the go, enhancing workplace flexibility.
- Automation: Automation in inventory management – from tracking incoming shipments to managing reorder alerts – saves time and reduces human error. Software that can automate routine tasks will allow employees to focus on more complex challenges in the manufacturing process.
These advancements in software development will invariably improve the operational effectiveness of manufacturers. The connectivity between software and technology is vital, creating a seamless experience that allows for tailored solutions to meet specific industry needs.
"The future of inventory management isn't just about holding stock; it's about strategically aligning resources to meet market demands effectively."
As the industry moves forward, it is clear that integrating sophisticated inventory management systems like Zoho Inventory will be essential. Manufacturers must stay ahead of the curve, embracing these technologies and trends to not only survive but thrive in an ever-changing landscape.
Ending: The Impact of Zoho Inventory
In the ever-evolving realm of manufacturing, the significance of inventory management cannot be overstated. Zoho Inventory emerges as a powerful ally in this sector, shaping operations in ways that directly influence efficiency and productivity. This conclusion serves not just as a wrap-up but as a compelling reminder of the multifaceted advantages that come with the adoption of this software.
Reduced Errors
One of the standout impacts of Zoho Inventory is the reduction of errors in stock management. Manual entry and tracking can lead to costly mistakes. However, with features such as automated stock adjustments and real-time updates, businesses can maintain more accurate records. This accuracy not only streamlines operations but also enhances trust along the supply chain as partners become confident in on-time delivery and inventory levels.
Enhanced Decision-Making
Data-driven insights are crucial for manufacturers looking to stay competitive. Zoho Inventory provides valuable analytical tools that assist in forecasting and demand planning. The ability to analyze trends and adjust procurement accordingly can mean the difference between a smooth operation and one that’s mired in inefficiencies.
Scalability
As businesses grow, their inventory needs evolve. Zoho Inventory is designed to scale with the company. Without an excessive investment in new systems, manufacturers can easily adapt to increasing complexities by leveraging the different functionalities offered. This flexibility ensures that businesses not only keep up with demand but also optimize their inventory processes without missing a beat.
"The real power of Zoho Inventory lies in its ability to transform data into actionable insights, enabling manufacturing firms to proactively manage their inventory rather than reactively responding to issues."
Cost Efficiency
Cost reduction is yet another significant impact. By improving the accuracy of stock levels and streamlining order management, manufacturers can lessen overstocking and stockouts. This translates into cost savings, which can be redirected towards further innovation and improvement of processes.