Revolutionizing Manufacturing Training: Harnessing Information Visualization Techniques
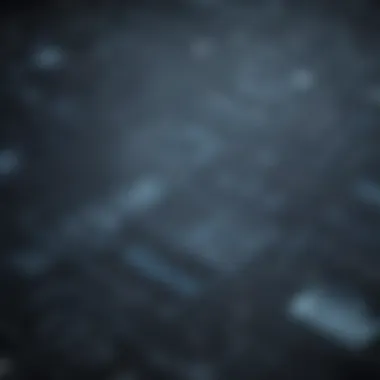
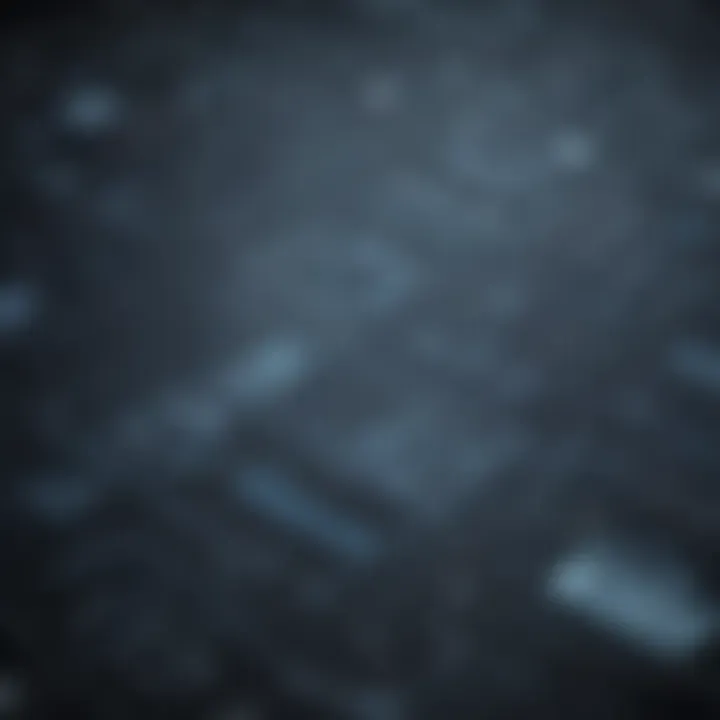
Software Overview
Pros and Cons
When delving into the software's strengths, it becomes evident that the visual aids offered greatly enhance learning outcomes. The incorporation of information visualization techniques leads to improved efficiency and accuracy in skill acquisition. However, every tool has its limitations. For instance, the software may be restricted in terms of scalability or customization options, constituting potential weaknesses. To gauge the software's efficacy, a comparison with similar products in the market can shed light on its unique selling points and areas for improvement.
Pricing and Plans
To ascertain the software's value proposition, evaluating the pricing and subscription options is inevitable. The diverse pricing plans available should align with the features and benefits offered by the software. A free trial or demo version grants users the opportunity to experience the software firsthand, facilitating informed decisions regarding its purchase. Determining whether the pricing is justifiable in relation to the software's capabilities is crucial in assessing its overall affordability.
Expert Verdict
Introduction
In the realm of manufacturing, the utilization of information visualization techniques holds paramount importance in transforming traditional training processes. By incorporating visual aids in training programs, organizations can enhance efficiency, accuracy, and overall learning outcomes for employees. This pivotal shift towards visual learning methodologies represents a cutting-edge approach to skill acquisition and retention, revolutionizing the way manufacturing workforce acquires essential competencies.
The Role of Information Visualization in Manufacturing Training
Understanding the concept of information visualization
Delving into the core essence of information visualization unveils its intrinsic ability to convey complex data in a visually digestible format. The essence lies in presenting intricate information through graphical representations, facilitating enhanced cognition and comprehension among learners. The distinctive feature of information visualization lies in its capacity to transform data into interactive visuals, fostering a more engaging and immersive learning experience. This unique characteristic enables learners to grasp abstract concepts more effectively, making it a preferred choice for optimizing manufacturing training processes remarkably.
Significance of visual learning in training
The significance of visual learning in training manifests in its capability to cater to diverse learning styles, ensuring that information is delivered in a universally accessible manner. Visual aids serve as potent tools for knowledge retention, as they stimulate multiple senses simultaneously, reinforcing learning through a multi-dimensional approach. The broad appeal of visual learning stems from its capacity to simplify complex ideas into easily understandable representations, transcending language and cognitive barriers. However, while visual learning enhances engagement and comprehension, potential disadvantages may arise in terms of over-reliance on visuals, potentially hindering the development of other cognitive skills in manufacturing training.
Objectives of the Article
Highlight the benefits of visual training in manufacturing
One key objective of this article is to illuminate the myriad benefits associated with integrating visual training methodologies in manufacturing education. From improved knowledge retention to enhanced engagement and comprehension, visual training stands out as a transformative approach to cultivate essential skills effectively. The pivotal characteristic of visual training lies in its capacity to bridge the gap between theoretical concepts and practical application, fostering a holistic learning experience that resonates long after the training sessions.
Explore practical applications of information visualization
Beyond highlighting the benefits, this article is geared towards exploring the practical applications of information visualization in the realm of manufacturing training. By delving into real-world examples and scenarios, readers will gain insights into how visual aids can streamline complex processes, minimize errors, and facilitate real-time decision-making. The unique feature of practical applications of information visualization lies in their ability to create immersive simulated environments that mimic real-world challenges, providing learners with hands-on experiences that transcend traditional training approaches.
Current Challenges in Manufacturing Training
Manufacturing training faces various challenges that demand attention. The intricacies in the training materials present a significant obstacle, with dense textual content being a primary concern. The sheer volume of information couched in text-heavy formats hampers effective learning. Learners are inundated with information, making comprehension and retention arduous. The need to decipher complex textual data poses a challenge in ensuring that the training content is absorbed optimally. Furthermore, the diversity of learning styles within manufacturing settings adds another layer of complexity. Individuals possess varying preferences and strategies for acquiring information, necessitating diverse approaches to cater to these differences.
Complexity of Training Materials
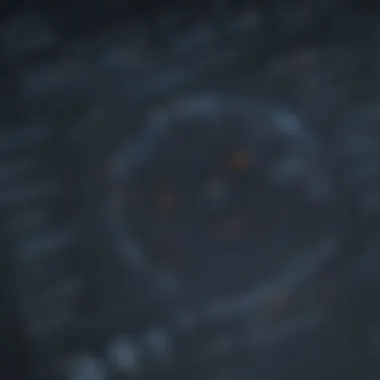
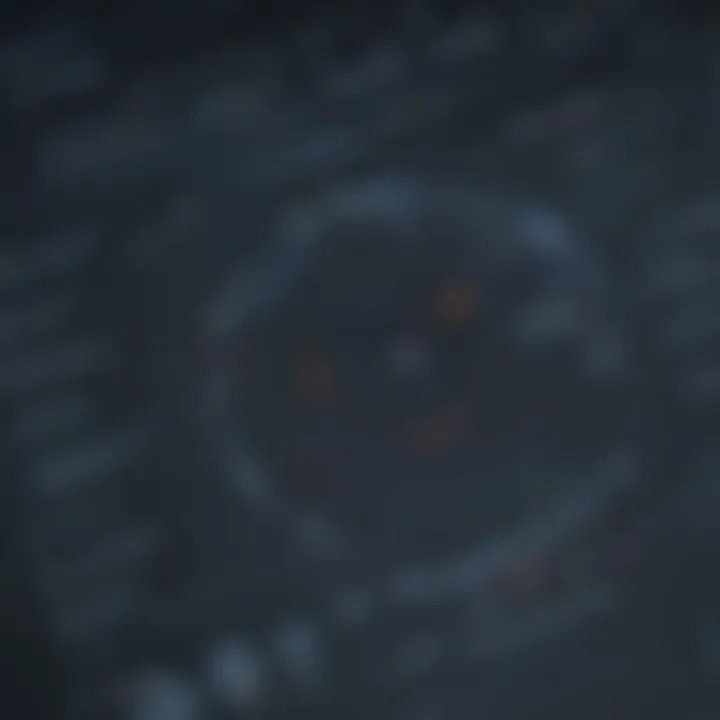
Impact of dense textual content
The impact of dense textual content in manufacturing training is profound. It serves as a fundamental element defining the challenges faced in disseminating knowledge effectively. The choice to utilize densely worded materials stems from the desire to provide comprehensive information; however, this approach can inadvertently hinder learning outcomes. The reliance on text-heavy resources limits engagement and makes it difficult for learners to grasp and retain crucial information. While text has traditionally been a prevalent mode of content delivery, its deficiencies in capturing and maintaining attention hinder the efficacy of training programs.
Diversity of learning styles
Within manufacturing training, the diversity of learning styles emerges as a critical factor influencing the effectiveness of educational initiatives. Understanding and accommodating various learning preferences is vital to engage all trainees optimally. Visual, auditory, readingwriting, and kinesthetic learners each necessitate tailored approaches to maximize their learning potential. Fostering a versatile learning environment that caters to these diverse styles enhances overall comprehension and knowledge retention. However, balancing these different styles poses a considerable challenge, requiring strategic planning to ensure comprehensive skill transfer.
Retention and Application of Knowledge
Retention of knowledge is a pivotal aspect of successful manufacturing training. Issues with knowledge retention plague conventional training methods, often resulting in suboptimal outcomes. The episodic nature of training sessions, coupled with memory decay over time, contributes to knowledge loss. Inadequate reinforcement mechanisms further exacerbate this challenge, impeding the ability of employees to recall and apply acquired information effectively. Transitioning theoretical understanding into practical skills represents a separate obstacle in the training process. The gap between conceptual comprehension and skill execution necessitates targeted interventions to bridge this divide.
Issues with knowledge retention
Knowledge retention issues within manufacturing training impede the long-term proficiency of employees. Absorbing information during training sessions is only half the battle; retaining and recalling this knowledge is equally critical. The transient nature of memory necessitates continuous reinforcement strategies to embed learned concepts into long-term memory. Failure to address retention issues leads to diminishing skill retention and subpar performance outcomes within manufacturing settings.
Translating theoretical understanding into practical skills
Translating theoretical knowledge into practical applications poses a formidable challenge in manufacturing training. Understandably, grasping theoretical concepts differs significantly from effectively applying them in real-world scenarios. Achieving a seamless transition from understanding to implementation demands targeted training strategies that simulate authentic work conditions. Practical exercises and real-world simulations play a vital role in enabling employees to bridge the gap between theoretical knowledge and practical competencies.
Training Program Adaptability
Enhancing training program adaptability holds paramount importance in optimizing instructional methodologies. The flexibility of training methods is instrumental in accommodating diverse learning needs and preferences. Tailoring training approaches to cater to individual learning paces is imperative for ensuring that all employees receive personalized instruction. Adaptability fosters an inclusive learning environment that accounts for the distinct requirements of each trainee, enhancing overall training effectiveness.
Flexibility in training methods
Flexibility in training methods allows for the customization of learning experiences to suit individual preferences and aptitudes. The adaptability of training modules ensures that information is delivered in diverse formats, catering to different learning styles. Incorporating varied approaches, such as interactive sessions, practical demonstrations, and visual aids, enriches the training experience and promotes comprehensive skill acquisition. The ability to adjust the pace and content of training programs according to individual needs contributes to a more engaging and impactful learning process.
Addressing individual learning pace
Addressing the diverse learning paces of employees is essential in fostering an inclusive and effective training environment. Recognizing that individuals progress and absorb information at differing rates underscores the importance of personalized instruction. Acknowledging and accommodating variations in learning speeds ensures that all employees receive adequate attention and support throughout their training journey. Tailoring the pace of instruction to align with individual capabilities promotes a conducive learning atmosphere where each employee can thrive and maximize their learning potential.
Benefits of Information Visualization in Manufacturing Training
Information visualization plays a pivotal role in transforming manufacturing training by enhancing learning experiences, efficiency, and accuracy. Visual aids not only optimize skill acquisition but also revolutionize the effectiveness of training programs. By leveraging information visualization, organizations can significantly improve their training methodologies and outcomes. Visual representations simplify complex concepts, making them more digestible for trainees. This section delves into the critical aspects of integrating information visualization in manufacturing training.
Enhanced Learning Experience
Improved Comprehension and Information Retention
Enhanced comprehension and information retention are key pillars of effective training. By presenting information visually, learners can grasp and retain content more efficiently. Visual aids help in breaking down intricate topics into simpler components, facilitating better understanding and knowledge retention. The utilization of visual learning methods enhances skill acquisition and long-term retention, contributing to the overarching goal of the training program.
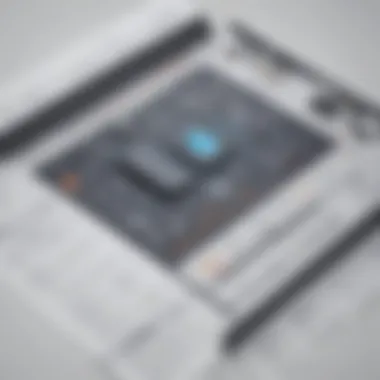
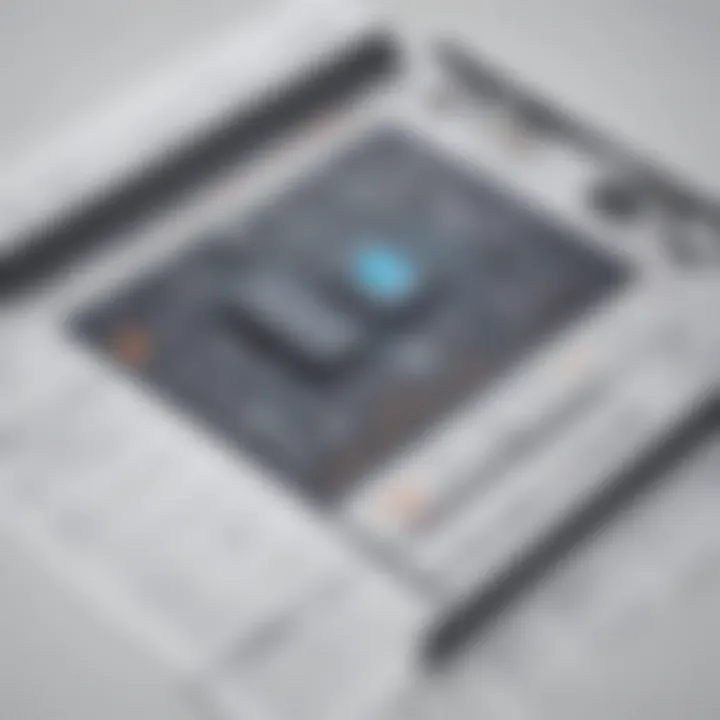
Engagement through Interactive Visual Aids
Engagement is paramount in effective training, and interactive visual aids foster a dynamic learning environment. Through interactive elements, such as simulations and virtual scenarios, trainees actively participate in the learning process. Interactive visual aids not only maintain engagement but also promote active participation and exploration. This section explores the benefits and considerations of incorporating interactive visual aids to enrich the learning experience in manufacturing training.
Efficiency and Accuracy
Streamlining Complex Processes
Streamlining complex processes through visual representations simplifies workflows and enhances efficiency. By visually mapping out procedures and workflows, trainees can navigate through tasks with clarity and precision. Visual tools streamline the learning process, making it more structured and coherent. The streamlined approach not only saves time but also minimizes errors, contributing to improved overall efficiency within the manufacturing training environment.
Reducing Errors in Task Execution
Error reduction is crucial in manufacturing training to ensure quality and proficiency. Visual cues and prompts help in minimizing errors during task execution by providing clear guidance and instructions. By visualizing potential pitfalls and common errors, trainees can proactively address challenges. Reducing errors leads to improved task accuracy and adherence to quality standards, reinforcing the significance of visual aids in manufacturing training.
Real-time Data Visualization
Monitoring Performance Metrics
Monitoring performance metrics in real-time offers valuable insights into trainees' progress and proficiency levels. Visualizing performance data enables trainers to assess individual performance and identify areas of improvement. Real-time data visualization empowers trainers to make data-driven decisions, enhancing the overall training experience. This section analyzes the impact and benefits of monitoring performance metrics through visual representations in manufacturing training.
Identifying Areas for Improvement
Identifying areas for improvement through data visualization facilitates targeted interventions and personalized training plans. Visual representations highlight areas of strength and weaknesses, enabling trainers to tailor training programs accordingly. By visualizing areas for improvement, organizations can optimize training strategies and maximize learning outcomes. This segment explores the advantages and considerations of utilizing visual data to identify and address areas for improvement in manufacturing training.
Practical Applications of Information Visualization in Manufacturing Training
Information visualization plays a pivotal role in enhancing manufacturing training by offering a visually engaging learning experience that fosters comprehension and knowledge retention. By incorporating visual elements into training programs, organizations can streamline complex processes and reduce errors, ultimately improving efficiency and accuracy. Practical applications of information visualization in manufacturing training encompass simulated training environments, interactive training modules, and performance monitoring dashboards.
Simulated Training Environments
Virtual reality simulations
Virtual reality simulations are a key component of practical applications in manufacturing training. These simulations provide a unique immersive experience that allows trainees to engage with real-life scenarios in a controlled virtual environment. The benefit of virtual reality simulations lies in their ability to offer hands-on training without the need for physical equipment or resources, making them a cost-effective and efficient choice for organizations looking to elevate their training methodologies. However, challenges such as the initial setup costs and technological requirements may pose limitations to widespread adoption.
Hands-on experiential learning
Hands-on experiential learning is another critical aspect of simulated training environments. This approach enables trainees to actively participate in tasks and exercises, promoting experiential learning that enhances skill acquisition and knowledge retention. The key characteristic of hands-on experiential learning is its practical orientation, allowing trainees to apply theoretical concepts in real-world scenarios. While hands-on learning fosters hands-on skills development, it may require substantial resources and time commitment to design and implement effectively.
Interactive Training Modules
Gamification for skill development
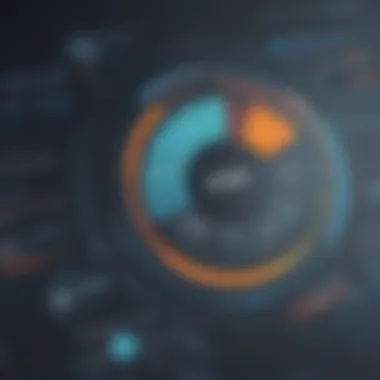
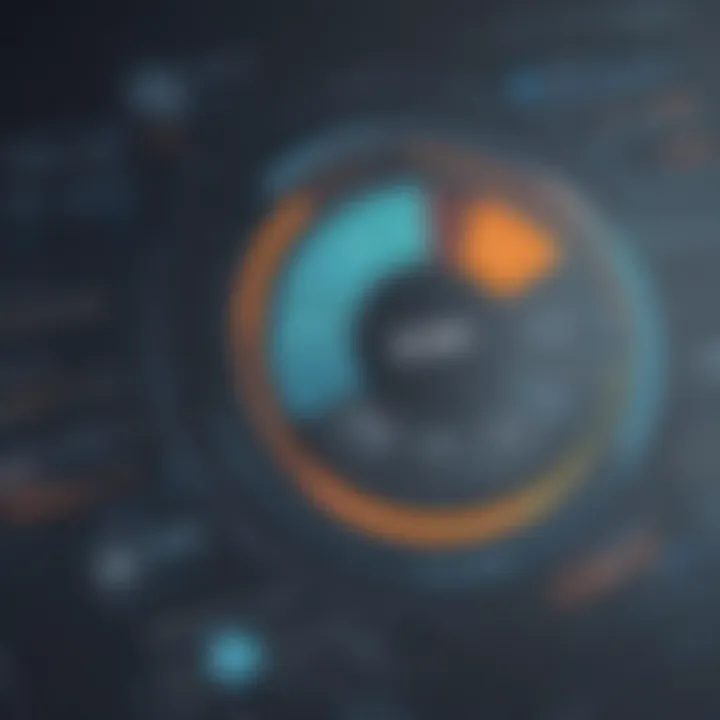
Interactive training modules often leverage gamification techniques to engage trainees and enhance skill development. Gamification incorporates game elements such as rewards, points, and challenges into training modules, increasing motivation and participation. The unique feature of gamification is its ability to transform learning into a competitive and interactive experience, driving trainees to actively seek knowledge and skill improvement. However, the effectiveness of gamification relies on thoughtful design and alignment with learning objectives to ensure meaningful outcomes.
Scenario-based learning exercises
Scenario-based learning exercises present trainees with situational challenges that simulate real-world scenarios, fostering critical thinking and decision-making skills. The key characteristic of scenario-based learning is its focus on practical application and problem-solving, allowing trainees to directly apply their learning in relevant contexts. While scenario-based exercises promote experiential learning and skill transfer, designing authentic and effective scenarios requires careful planning and evaluation to deliver impactful training results.
Performance Monitoring Dashboards
Visualizing individual progress
Performance monitoring dashboards offer trainees and instructors real-time insights into individual progress and performance metrics. Visualizing individual progress through charts, graphs, and data analytics allows for personalized feedback and goal tracking, empowering trainees to monitor their development. The key characteristic of visualizing individual progress is its transparency and accountability, enabling trainees to track their performance objectively and identify areas for improvement. However, clarity in data presentation and meaningful interpretation are crucial for effective utilization of performance dashboards.
Aggregate data analysis for insights
Aggregate data analysis within performance monitoring dashboards provides organizations with valuable insights into training effectiveness and overall performance trends. By analyzing aggregated data from multiple trainees, organizations can identify patterns, strengths, and areas for improvement at a broader level. The unique feature of aggregate data analysis is its capability to offer strategic insights for decision-making and curriculum enhancement. However, ensuring data accuracy, confidentiality, and relevance remains critical for leveraging aggregate data effectively in training evaluation and improvement.
Section 5: Implementation Strategies for Visual Manufacturing Training
In this section, we will elaborate on the crucial element of Implementation Strategies for Visual Manufacturing Training in optimizing training processes. It is pertinent to understand the specific elements, benefits, and considerations associated with Implementation Strategies as they play a pivotal role in enhancing learning outcomes.
Integration with Learning Management Systems
Seamless incorporation of visual modules
The seamless integration of visual modules within Learning Management Systems holds paramount importance in the effectiveness of training programs. By smoothly incorporating visual aids, organizations can facilitate better understanding and engagement among trainees. This seamless integration ensures that visual modules do not disrupt the flow of the training but enhance it. The key characteristic of seamless incorporation is its ability to blend visual elements without causing distractions or complications, making it a popular choice within this article. The unique feature of seamless integration lies in its capacity to unify textual content with visual representations seamlessly. While its advantages include improved comprehension and engagement, a potential disadvantage could be the need for compatibility with various devices or platforms.
Tracking and assessment capabilities
The integration of tracking and assessment capabilities within Learning Management Systems enables organizations to monitor the progress and performance of trainees effectively. By tracking individual learning pathways and behavior, organizations can tailor training programs to meet specific needs and enhance overall outcomes. The key characteristic of tracking and assessment lies in its provision of data-driven insights that guide training improvement strategies. It is a beneficial choice for this article as it emphasizes the importance of measuring the effectiveness of visual training methods. The unique feature of tracking and assessment capabilities is their ability to provide real-time feedback on trainee performance, allowing for immediate adjustments. While the advantages include personalized learning experiences and targeted feedback, a potential disadvantage could be the requirement for advanced analytics tools or technologies.
Collaborative Training Platforms
Virtual teamwork exercises
Virtual teamwork exercises contribute significantly to the overall objective of enhancing manufacturing training through collaboration and interactive learning. These exercises simulate real-world working environments where employees can engage and collaborate virtually, fostering teamwork and problem-solving skills. The key characteristic of virtual teamwork exercises is their ability to connect geographically dispersed teams and cultivate a shared learning experience. This aspect makes it a beneficial choice for this article as it emphasizes the importance of collaborative learning in manufacturing contexts. The unique feature of virtual teamwork exercises is their capacity to promote cross-functional collaboration and communication through digital platforms. While the advantages include enhanced teamwork skills and remote work readiness, a potential disadvantage could be the challenges in coordinating time zones and technology access.
Knowledge sharing through visual mediums
Knowledge sharing through visual mediums is instrumental in promoting information dissemination and transfer within manufacturing training programs. By utilizing visual aids to convey complex concepts and procedural guidelines, organizations can enhance knowledge retention and understanding among employees. The key characteristic of knowledge sharing through visual mediums is its capacity to simplify abstract information into digestible visual formats, making it a popular choice for this article. The unique feature lies in its ability to cater to varied learning styles and preferences, ensuring that information is effectively communicated to diverse audiences. While the advantages include improved information retention and engagement, a potential disadvantage could be the reliance on visual literacy skills among trainees.
Continuous Improvement Mechanisms
Feedback loops for content enhancement
Feedback loops play a critical role in refining and enhancing training content to meet the evolving needs of employees. By collecting feedback from trainees regarding the effectiveness of visual training materials, organizations can iterate and improve content quality. The key characteristic of feedback loops is their iterative nature, allowing for continuous enhancement based on real-time input. It is a beneficial choice for this article as it emphasizes the importance of incorporating feedback mechanisms within visual training programs. The unique feature of feedback loops is their capacity to create a culture of continuous improvement and innovation in training methodologies. While the advantages include tailored learning experiences and iterative content development, a potential disadvantage could be the time and resources required to implement feedback collection and analysis.
Iterative design for optimized learning outcomes
Implementing iterative design approaches in manufacturing training programs is essential for achieving optimal learning outcomes. By continuously refining and adapting visual training materials based on performance data and feedback, organizations can ensure the efficacy of their training programs. The key characteristic of iterative design is its focus on iteration and experimentation to drive continuous improvement in learning experiences. This aspect makes it a valuable choice for this article as it underscores the importance of adaptability and optimization in manufacturing training. The unique feature of iterative design lies in its emphasis on data-driven decision-making and evidence-based design strategies. While the advantages include personalized learning paths and responsive training content, a potential disadvantage could be the need for regular updates and revisions to training materials.