Maximizing Efficiency: A Comprehensive Guide to Optimizing MES Systems in Manufacturing
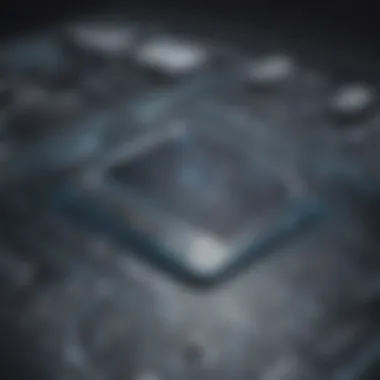
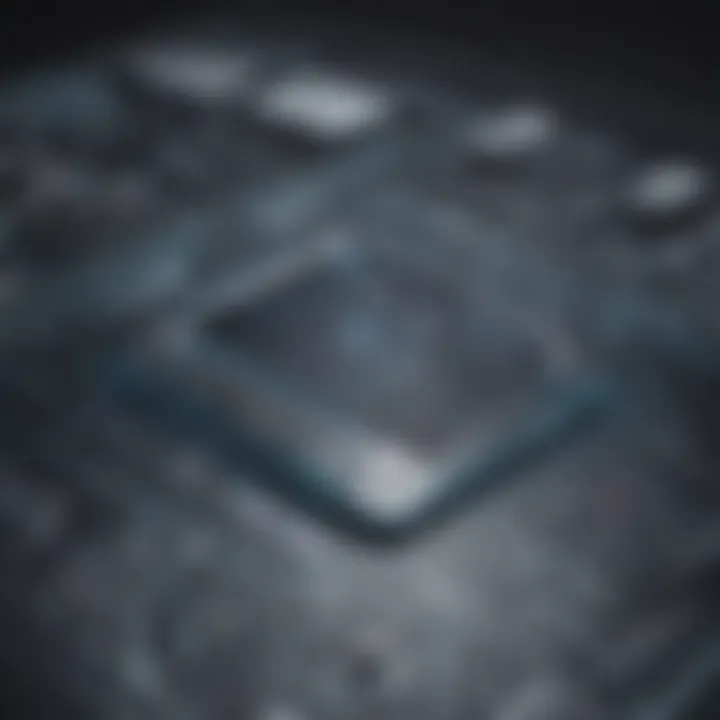
Software Overview
In this section, we will delve into the intricate details of MES systems in the manufacturing industry. These systems play a pivotal role in streamlining production processes, enhancing efficiency, and optimizing resource utilization. By understanding the features and functionalities of MES software, users can harness its full potential to boost productivity on the manufacturing floor. Exploring the user interface and navigation aspects will shed light on the ease of use and overall user experience, which are essential considerations for seamless integration into existing operations. Furthermore, we will also discuss compatibility and integrations to gauge the software's versatility in connecting with different devices and other software systems.
Pros and Cons
As we evaluate MES systems, it's crucial to delineate their strengths and weaknesses. The strengths revolve around the significant advantages and benefits they offer, such as real-time production monitoring, data analytics for informed decision-making, and standardized processes for consistency. Conversely, we must address any weaknesses or limitations, such as potential implementation complexities or adaptability challenges. By providing a comparison with similar software products, we can discern the unique selling points and areas for improvement, facilitating informed decision-making for potential users.
Pricing and Plans
The pricing and plans aspect of MES systems is pivotal for potential adopters. Detailing the subscription options will enable users to choose a plan that aligns with their specific requirements and budget constraints. Moreover, mentioning the availability of a free trial or demo version can expedite the decision-making process by allowing hands-on exploration of the software's features. Evaluating the value for money entails a holistic approach, considering the pricing vis- o-vis the features and benefits offered, ensuring transparency and adequacy in the pricing structure.
Expert Verdict
In the final section, we provide an expert verdict on optimizing MES systems in manufacturing. Offering conclusive thoughts and recommendations based on the detailed analysis, we aim to guide users towards informed choices regarding software adoption. By delineating the target audience suitability, we provide insights into which demographic stands to benefit most from utilizing MES systems, such as software developers, IT professionals, and students seeking industry-relevant skills. Speculating on potential future updates underscores the software's adaptability and responsiveness to evolving industry demands, ensuring its relevance and competitiveness in the dynamic manufacturing landscape.
Introduction to MES Systems
MES systems play a crucial role in modern manufacturing, revolutionizing how production processes are managed and optimized. Understanding the significance of MES systems is paramount for enhancing operational efficiency and productivity on the factory floor. By delving into the core functions and capabilities of MES systems, businesses can streamline their processes, improve decision-making, and drive overall performance.
Understanding MES Systems
The role of MES systems in modern manufacturing:
MES systems act as a central nervous system for manufacturing operations, orchestrating production activities, monitoring performance metrics, and facilitating real-time decision-making. Their ability to collect, analyze, and disseminate data across various functions enables seamless coordination and synchronization of processes. This proactive approach enhances operational visibility, accelerates problem resolution, and ultimately boosts productivity.
Key components of MES systems:
Key components of MES systems include production scheduling, resource allocation, quality management, and reporting tools. These elements work in conjunction to optimize manufacturing processes, minimize downtime, and ensure consistent product quality. Their integration with other systems like ERP and Io T further enhances data accuracy and operational efficiency, making them indispensable in the manufacturing landscape.
Benefits of implementing MES systems:
Implementing MES systems offers a myriad of benefits, including improved production efficiency, enhanced quality control, reduced lead times, and better resource utilization. By leveraging MES functionalities, manufacturers can proactively address bottlenecks, mitigate risks, and meet customer demands effectively. The granular insights provided by MES systems empower organizations to drive continuous improvement initiatives, capitalize on opportunities, and stay ahead in today's competitive market.
Evolution of MES Systems
From traditional manufacturing to digital transformation:
The evolution of MES systems from traditional paper-based methods to digital platforms signifies a paradigm shift in manufacturing processes. It denotes a transition towards data-driven decision-making, automation, and connectivity, fostering agility and scalability in operations. This evolution underscores the imperative for manufacturers to embrace technological advancements for sustainable growth and competitiveness.
Impact of Industry on MES systems:
The advent of Industry 4.0 has catalyzed a transformation in MES systems, aligning them with interconnected smart manufacturing environments. Integration of Io T, AI, and cloud computing technologies into MES systems has revolutionized data analytics, predictive maintenance, and adaptive production strategies. This convergence has not only optimized operational efficiencies but also paved the way for predictive and prescriptive analytics, heralding a new era of smart manufacturing.
Future trends in MES system development:
The future of MES systems lies in harnessing AI, machine learning, and predictive analytics to create self-learning and responsive production ecosystems. Advanced features such as digital twins, augmented reality interfaces, and edge computing capabilities are shaping the next generation of MES solutions. These innovations are poised to drive greater automation, agility, and customization in manufacturing processes, setting the stage for unprecedented levels of operational excellence and business success.
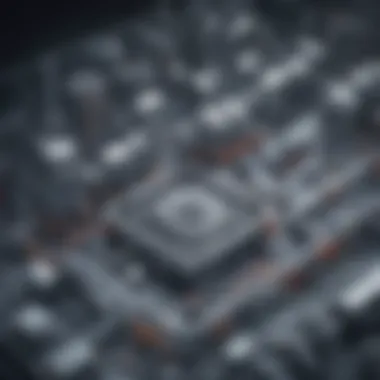
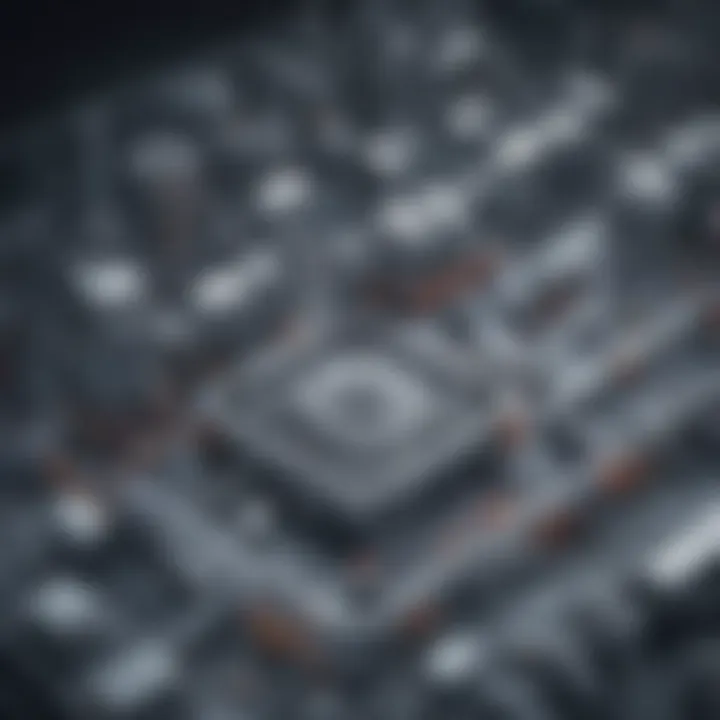
Integration of MES Systems
In the realm of the manufacturing industry, the Integration of MES Systems plays a pivotal role in streamlining operations and enhancing efficiency. By seamlessly connecting Manufacturing Execution Systems (MES) with other software systems, companies can achieve synchronization across various departments. This integration is not merely a technological advancement but a strategic move towards improving overall productivity and decision-making processes. Key elements such as real-time data exchange, process automation, and resource optimization are fundamental benefits derived from integrating MES systems. When MES Systems and other software applications work in harmony, businesses can experience smoother production flows, reduced downtime, and enhanced data accuracy.
MES Systems and IoT
The synergy between MES systems and Io T: Within the context of manufacturing, the collaboration between MES systems and the Internet of Things (IoT) offers unparalleled possibilities for data collection and analysis. This synergy enables seamless connectivity between machines, sensors, and MES platforms, facilitating real-time monitoring and advanced analytics. The key characteristic of this synergy lies in its ability to provide a holistic view of the production process, allowing for predictive maintenance and proactive decision-making. The unique feature of MES-IoT integration is the enhanced visibility it provides into every aspect of manufacturing, leading to optimized production outcomes. While advantageous in improving operational efficiency and quality control, challenges may arise in managing the vast amounts of data generated and ensuring data security.
Enhancing data-driven decision-making: One specific aspect of integrating MES systems with Io T is the enhancement of data-driven decision-making processes. By leveraging IoT devices and MES platforms, manufacturers can access comprehensive datasets in real time, enabling them to make informed decisions promptly. This approach enhances operational agility and responsiveness to market fluctuations, giving companies a competitive edge. The uniqueness of this feature lies in its ability to transform raw data into actionable insights, empowering organizations to identify trends, detect anomalies, and optimize processes efficiently. While advantageous in improving decision-making accuracy, potential disadvantages may include data overload and the need for advanced analytics capabilities.
Case studies on successful MES-Io T integration: Examining successful implementations of MES-IoT integration showcases the practical benefits and outcomes of this strategic alignment. Through detailed case studies, manufacturers can learn from real-world examples of how MES and IoT collaboration has revolutionized production environments. These case studies highlight the positive impact on operational efficiency, quality enhancement, and resource utilization achieved through MES-IoT integration. By delving into specific instances of successful integration, companies can glean valuable insights into best practices, challenges faced, and solutions implemented, paving the way for their own successful integration journey.
Interfacing with ERP Systems
Seamless communication between MES and ERP systems: The efficient communication between MES and ERP systems is critical for ensuring a hassle-free flow of information and data exchange in manufacturing environments. Seamless integration allows for real-time updates on production schedules, inventory status, and resource availability, enabling better decision-making processes. The key characteristic of seamless communication lies in the synchronization of operational data between MES and ERP systems, eliminating discrepancies and enhancing overall operational visibility. This integration choice is beneficial for this article as it underlines the importance of data coherence across different functional areas, driving operational excellence and strategic alignment. Despite its benefits, challenges such as system compatibility, data mapping complexities, and cybersecurity risks must be effectively addressed to maximize the advantages of integration.
Optimizing resource planning and production scheduling: Another critical aspect of integrating MES with ERP systems is the optimization of resource planning and production scheduling. By combining MES functionalities with ERP capabilities, companies can achieve a comprehensive view of their manufacturing operations, from shop floor activities to enterprise-wide resource allocation. The advantageous aspect of this integration is the ability to synchronize production schedules, material requirements, and workforce assignments, ensuring efficient resource utilization and timely order fulfillment. The unique feature of this optimization lies in its proactive approach to demand forecasting, capacity planning, and inventory management, resulting in reduced lead times and improved customer satisfaction. However, challenges may arise in data consistency, complexity of planning algorithms, and adapting to dynamic market conditions.
Challenges and solutions in integration: Addressing the challenges encountered during the integration of MES and ERP systems is crucial for mitigating risks and ensuring successful implementation. Companies may face issues such as data migration complexities, system interoperability challenges, and process alignment differences that can impede seamless integration. By identifying these challenges proactively, organizations can implement robust solutions such as data mapping tools, middleware integration platforms, and cross-functional collaboration strategies. The key characteristic of tackling integration challenges lies in the recognition of system dependencies, process interdependencies, and organizational readiness for change. While integrating MES and ERP systems offers numerous advantages, including streamlined operations and enhanced decision-making, overcoming integration challenges requires a systematic approach and holistic perspective towards aligning people, processes, and technologies for sustainable success.
Optimization Strategies for MES Systems
In this 'Optimizing MES Systems in Manufacturing' guide, a significant focus is placed on optimizing MES systems within manufacturing operations, emphasizing the crucial role of efficient strategies to enhance productivity and streamline processes. Optimization Strategies for MES Systems form the backbone of modern manufacturing, enabling companies to stay competitive in an ever-evolving industry landscape. By implementing advanced optimization techniques, businesses can achieve operational excellence, cost-efficiency, and improved production output.
Real-Time Data Analytics
Utilizing real-time data for process optimization
The utilization of real-time data for process optimization is a fundamental aspect of enhancing manufacturing operations. By leveraging real-time data insights, businesses can make informed decisions promptly, identify areas for improvement, and optimize processes efficiently. Real-time data analytics contribute to proactive decision-making, enabling companies to respond promptly to fluctuations in demand, minimize downtime, and maximize production output. The ability to access and analyze data in real-time ensures that manufacturing processes remain agile, adaptive, and aligned with business goals.
Predictive maintenance and quality control
Predictive maintenance and quality control play a pivotal role in optimizing MES systems. By implementing predictive maintenance strategies, companies can preemptively address equipment failures, minimize unplanned downtime, and ensure continuous operations. Quality control mechanisms integrated into MES systems enable real-time monitoring of production processes, facilitating early detection of deviations and anomalies. This proactive approach to maintenance and quality control enhances overall equipment effectiveness and product quality, contributing to sustainable operational excellence.
Continuous improvement through data analysis
Continuous improvement through data analysis is a cornerstone of modern manufacturing optimization. By continuously analyzing and interpreting data generated within MES systems, companies can identify trends, patterns, and inefficiencies, driving ongoing process enhancements. Data analysis provides a holistic view of manufacturing operations, empowering businesses to fine-tune processes, eliminate bottlenecks, and enhance overall efficiency. The iterative nature of continuous improvement ensures that manufacturing operations remain agile, adaptive, and optimized for sustained success.
Challenges and Best Practices
When delving into the world of MES systems within the manufacturing realm, understanding the critical aspects of challenges and best practices becomes paramount. The optimization of MES systems requires a keen awareness of potential roadblocks and opportunities for improvement. By focusing on challenges and best practices, organizations can streamline their operations, enhance productivity, and ensure a smooth transition towards optimized manufacturing processes.
Cybersecurity in MES Systems
Securing Manufacturing Data and Processes
In the context of MES systems, securing manufacturing data and processes plays a significant role in safeguarding critical information and ensuring operational integrity. The emphasis on securing data within manufacturing environments is crucial due to the sensitive nature of proprietary data and production processes. By implementing robust security measures, organizations can mitigate the risk of data breaches and unauthorized access, thereby protecting their assets and maintaining trust with stakeholders. The unique feature of securing manufacturing data lies in its ability to create a secure environment for sensitive information, minimizing the likelihood of cyber threats.
Preventing Cyber Threats and Vulnerabilities
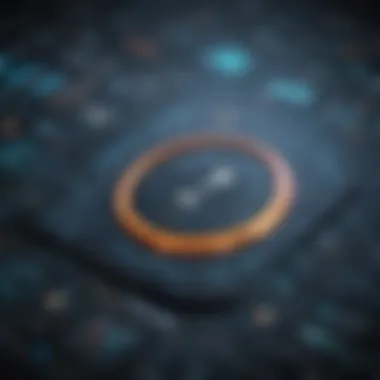
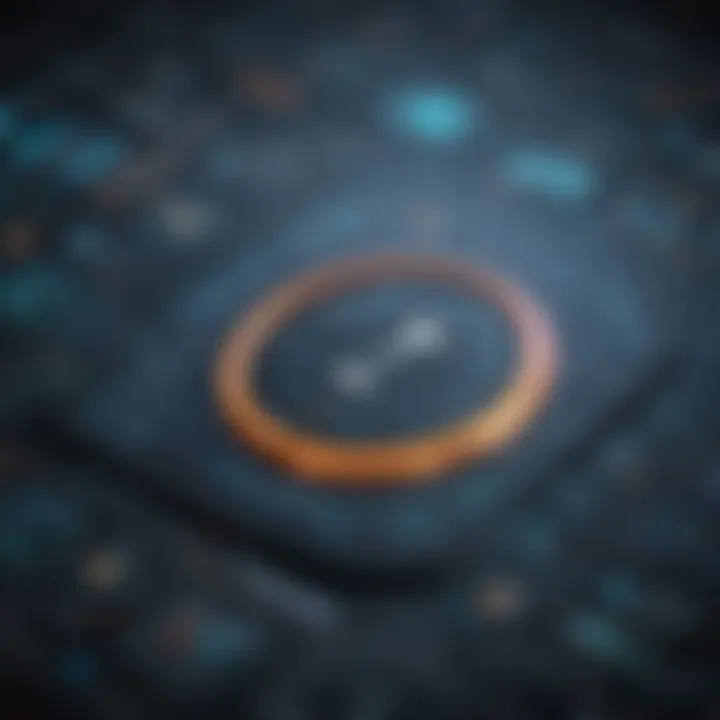
Preventing cyber threats and vulnerabilities is another essential aspect of cybersecurity within MES systems. Proactively identifying and addressing potential vulnerabilities helps organizations fortify their defenses against malicious attacks and cyber intrusions. By staying ahead of emerging threats and vulnerabilities, businesses can preemptively protect their systems and data from exploitation. The key characteristic of this practice lies in its proactive approach to cybersecurity, aiming to prevent breaches rather than react after an incident occurs. While this proactive stance offers numerous benefits, such as reduced downtime and financial losses, organizations must also consider the potential limitations in detecting rapidly evolving threats.
Strategies for Robust Cybersecurity Measures
Strategies for robust cybersecurity measures encompass a comprehensive approach to protecting MES systems from various cyber threats. From implementing encryption protocols to regular security assessments, these strategies aim to create a resilient security posture for manufacturing operations. The key characteristic of these measures is their multi-layered approach, combining technical solutions, employee training, and incident response protocols to address diverse cybersecurity challenges. While these strategies enhance overall security and reduce vulnerability, organizations must also allocate resources effectively to maintain these measures and adapt to evolving cybersecurity landscapes.
Change Management in MES Implementation
Overcoming Resistance to MES Adoption
One of the critical challenges in MES implementation is overcoming resistance to change within the organization. Resistance can stem from various factors, including fear of job displacement, unfamiliarity with new technologies, or concerns about disrupting established workflows. Addressing resistance requires effective communication, stakeholder engagement, and demonstrating the benefits of MES adoption. The unique feature of overcoming resistance lies in the need for targeted strategies that align with organizational culture and values, fostering a positive attitude towards change. While successful adoption leads to improved efficiency and competitiveness, organizations must also address potential drawbacks, such as disruptions during the implementation phase.
Training and Upskilling for MES Integration
Training and upskilling initiatives are essential elements of successful MES integration, ensuring that employees possess the necessary skills to leverage MES systems effectively. By providing training programs tailored to different user groups, organizations can empower their workforce to embrace new technologies and workflows. The key characteristic of training and upskilling efforts is their focus on enhancing employee competencies and promoting a culture of continuous learning. While effective training yields benefits such as increased productivity and quality standards, organizations must also consider the time and resources required to implement these programs.
Ensuring Smooth Transition and User Acceptance
Ensuring a smooth transition and promoting user acceptance are crucial factors in the successful implementation of MES systems. Organizations must facilitate a seamless shift towards new processes, address user concerns, and provide adequate support during the transition phase. The unique feature of this aspect lies in its emphasis on user experience and change management practices that foster acceptance and engagement. While a smooth transition enhances operational efficiency and employee satisfaction, organizations must also address any potential challenges, such as resistance from certain user groups or integration issues with existing systems.
Case Studies and Success Stories
In the realm of Manufacturing Execution Systems (MES), case studies and success stories play a pivotal role in illustrating the practical applications and remarkable outcomes of implementing MES systems in real-world scenarios. These stories serve as empirical evidence of the effectiveness and value that MES systems can bring to manufacturing operations. By delving into specific cases, readers can grasp the tangible benefits and challenges associated with integrating MES into diverse manufacturing environments, offering invaluable insights into best practices and potential pitfalls. Case studies act as a bridge between theoretical knowledge and practical implementation, shedding light on how leading companies have leveraged MES systems to enhance their productivity and efficiency levels.
Leading Companies Implementing MES Systems
Tesla's Utilization of MES for Efficient Production
In the dynamic landscape of manufacturing, Tesla stands out as a pioneering force in utilizing MES for optimizing production efficiency. Tesla's approach to MES deployment revolves around harnessing real-time data analytics to fine-tune its manufacturing processes and ensure seamless operations. By integrating MES seamlessly into its production line, Tesla has been able to achieve unparalleled levels of efficiency and quality control, setting new benchmarks for the industry. The key characteristic of Tesla's MES utilization lies in its ability to synchronize diverse manufacturing tasks and facilitate proactive decision-making, ultimately leading to significant improvements in overall operational performance. Although Tesla's approach comes with undeniable advantages in terms of agility and adaptability, challenges related to scalability and cybersecurity must be carefully considered and addressed.
Toyota's Lean Manufacturing with MES Integration
Toyota's embrace of lean manufacturing principles harmonized with MES integration epitomizes a harmonious fusion of traditional manufacturing wisdom with cutting-edge technology. By incorporating MES into its lean production framework, Toyota has streamlined its operations, minimized waste, and optimized resource allocation, exemplifying the synergy between organizational efficiency and technological innovation. The distinctive feature of Toyota's approach lies in its emphasis on continuous improvement and employee involvement, fostering a culture of innovation and excellence. While Toyota's strategy yields multiple advantages in terms of cost-effectiveness and process optimization, complexities related to change management and integration bottlenecks must be managed effectively to maximize the benefits of MES incorporation.
Siemens' Innovative Approach to MES Optimization
Siemens' commitment to innovation reflects prominently in its approach to MES optimization, where cutting-edge technologies converge to redefine manufacturing paradigms. Siemens leverages a comprehensive suite of MES solutions to drive operational excellence, enhance decision-making processes, and empower manufacturers to adapt to dynamic market demands swiftly. The distinguishing feature of Siemens' methodology lies in its holistic view of MES integration, encompassing not only process optimization but also organizational transformation towards a digital future. While Siemens' innovative approach offers notable advantages in terms of flexibility and scalability, the intensive data requirements and potential interoperability issues necessitate a meticulous deployment strategy.
Impact of MES on Industry Performance
In the context of industry performance, the impact of MES systems reverberates across key metrics such as productivity enhancements, cost savings, and competitive advantage. By leveraging MES technologies, manufacturers can augment their operational efficiency, drive down production costs, and position themselves strategically in a competitive marketplace. The intrinsic value of MES systems lies in their capacity to orchestrate seamless workflows, optimize manufacturing processes, and empower organizations to achieve sustainable growth and resilience.
Productivity Enhancements Through MES Systems
Productivity enhancements through MES systems catalyze a paradigm shift in manufacturing efficiency, enabling companies to amplify their throughput rates, reduce downtime, and enhance product quality. The pivotal characteristic of productivity enhancements via MES stems from the ability to monitor production metrics in real-time, identify bottlenecks, and implement corrective measures promptly, thus fostering a culture of continuous improvement. While the advantages of productivity enhancements are manifold, challenges related to data integration and workforce reskilling must be navigated to unleash the full potential of MES-driven productivity gains.
Cost Savings and Resource Utilization
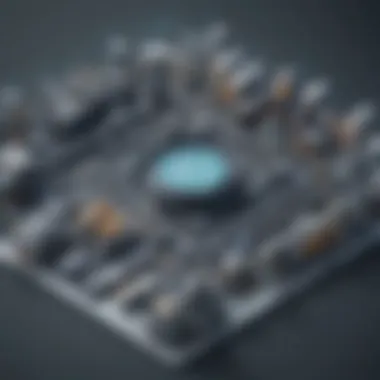
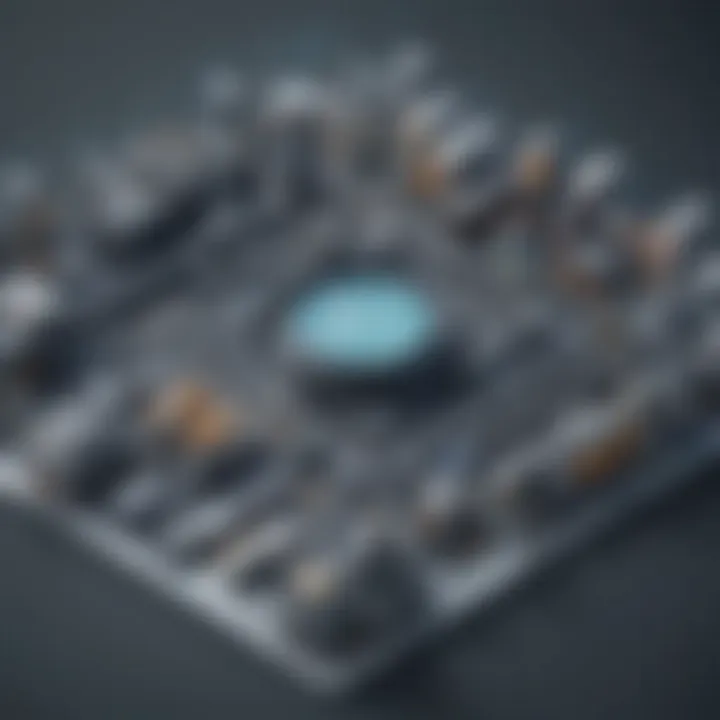
Cost savings and resource utilization represent fundamental pillars of MES's impact on industry performance, facilitating prudent resource allocation, budget optimization, and strategic decision-making. The cardinal virtue of cost savings and resource utilization through MES lies in the ability to streamline production processes, minimize overhead expenses, and capitalize on operational efficiencies to drive sustainable growth. Despite the undeniable advantages of cost savings and resource optimization facilitated by MES systems, the complexities inherent in system integration and data management necessitate a meticulous approach to implementation and oversight.
Competitive Advantage Achieved by MES Implementation
The competitive advantage derived from MES implementation underscores the transformative potential of MES systems in bolstering organizational agility, fostering innovation, and distinguishing companies in crowded marketplaces. By embracing MES technologies, companies can fortify their market position, respond adeptly to customer demands, and innovate proactively to stay ahead of the curve. The defining feature of competitive advantage through MES lies in its ability to harmonize data-driven decision-making with operational agility, empowering companies to outperform competitors and carve out a sustainable niche in the industry. While the benefits of competitive advantage are substantial, considerations around cybersecurity resilience and performance monitoring must be factored into the equation to safeguard sustained success.
Future Trends and Innovations
In the realm of MES system optimization, staying on top of future trends and innovations is crucial. Understanding the potential impact of emerging technologies is vital for enhancing manufacturing efficiency. By delving into the developments in AI and machine learning within MES systems, manufacturers can unlock new potentials. These advancements pave the way for predictive maintenance, process optimization through machine learning algorithms, and a transformative impact on future manufacturing processes. Companies that embrace AI-driven MES systems are likely to experience a significant competitive advantage, driving productivity and quality to new heights.
AI and Machine Learning in MES
Applications of AI for Predictive Maintenance
Exploring the incorporation of AI for predictive maintenance in MES systems reveals a groundbreaking approach to equipment upkeep. By leveraging AI algorithms, manufacturers can predict maintenance needs before failures occur, minimizing downtime and optimizing operational efficiency. The ability of AI to analyze vast amounts of data quickly sets it apart as a powerful tool in predictive maintenance, ensuring equipment reliability and longevity. However, challenges such as the initial setup and data calibration may hinder seamless integration but the long-term benefits outweigh these initial hurdles.
Machine Learning Algorithms for Process Optimization
Machine learning algorithms offer a data-driven approach to process optimization within MES systems. These algorithms continuously learn from data inputs, adjusting processes in real-time to maximize efficiency and quality. They excel in identifying patterns and anomalies, streamlining operational workflows, and adapting to fluctuating demands. The adaptability and precision of machine learning algorithms enhance production outcomes, though careful monitoring and fine-tuning are essential for optimal performance.
Impact of AI-Driven MES on Future Manufacturing
The integration of AI into MES systems elevates the future of manufacturing by revolutionizing decision-making processes and operational dynamics. AI-driven MES fosters adaptive production practices, predictive analysis for strategic planning, and efficient resource utilization. The seamless fusion of AI with MES systems optimizes production lines, ensures consistent quality standards, and empowers manufacturers to proactively address challenges. While adjusting to the complexities of AI implementation may require substantial resources and expertise, the rewards in productivity gains and competitive edge are well worth the investment.
Blockchain Integration in MES Systems
Enhancing Traceability and Transparency in Manufacturing
Implementing blockchain technology in MES systems enhances traceability and transparency throughout the manufacturing process. By recording each transaction as a block in a tamper-proof chain, manufacturers can track product movement, origin, and modifications securely. The immutable nature of blockchain ensures data integrity and authenticity, strengthening supply chain visibility and compliance. Despite its advantages, ensuring scalable blockchain integration and compatibility with existing systems pose adoption challenges demanding meticulous planning and execution.
Smart Contracts and Data Security in MES Operations
Smart contracts provide automated, secure agreements verifiable on the blockchain, streamlining transactions and enhancing data security. By facilitating self-executing contracts based on predefined conditions, smart contracts optimize workflow efficiency and reduce risks of fraud or errors. Their implementation in MES operations ensures data integrity, real-time tracking, and streamlined processes. However, despite their benefits, ensuring smart contract functionality aligns with operational requirements and complies with regulatory standards requires rigorous testing and validation.
Adoption Challenges and Benefits of Blockchain in MES
Integrating blockchain in MES systems not only presents benefits but also challenges in adoption. The decentralized nature of blockchain offers enhanced security, transparency, and decentralized decision-making, driving operational efficiencies. However, overcoming the learning curve, ensuring network scalability, and addressing regulatory compliance are critical challenges. Balancing the benefits of blockchain adoption with the potential risks demands a strategic approach and a clear understanding of the transformative impact on MES optimization.
Conclusion
In the realm of optimizing MES systems in manufacturing, it is imperative to grasp the significance of efficient conclusions. A robust conclusion serves as the final piece of the puzzle, summarizing the key takeaways and insights gained throughout the comprehensive guide. It encapsulates the essence of MES system optimization, emphasizing the need for continuous enhancement and strategic advancements to propel manufacturing operations forward. The conclusion section acts as a pivotal juncture to reflect on the importance of implementing MES systems and leveraging optimization strategies to drive productivity and efficiency in the manufacturing sector.
Key Takeaways
- Importance of MES systems in modern manufacturing
MES systems play a pivotal role in modern manufacturing, serving as the backbone of efficient production processes. The integration of MES systems streamlines operations, enhances decision-making capabilities, and improves overall productivity on the shop floor. One key characteristic of MES systems is their ability to provide real-time data analytics, enabling manufacturers to make informed decisions swiftly. This real-time visibility into production metrics and performance indicators is a crucial asset for optimizing processes and fostering continuous improvement. While MES systems offer significant advantages in operational transparency and resource utilization, challenges such as system integration and cybersecurity must be mitigated for seamless implementation.
- Continuous improvement through optimization strategies
Continuous improvement lies at the core of MES system optimization, fostering a culture of ongoing enhancements in manufacturing practices. By embracing lean manufacturing principles and automation technologies, organizations can streamline workflows, reduce waste, and enhance overall efficiency. Optimization strategies centered on predictive maintenance and quality control empower manufacturers to proactively address equipment failures and ensure product quality standards are met consistently. The journey towards optimizing MES systems involves continuous data analysis, feedback integration, and operational refinement to drive sustainable growth and operational excellence.
- Future implications and advancements in MES technology
The future landscape of MES technology unveils promising advancements that are poised to revolutionize manufacturing operations. As artificial intelligence and machine learning algorithms are integrated into MES systems, predictive maintenance capabilities and data-driven insights will catapult manufacturing efficiency to new heights. The convergence of blockchain technology with MES systems promises heightened traceability and security in manufacturing processes, paving the way for enhanced transparency and immutable data records. While the future implications of MES technology underscore unparalleled opportunities for industry growth and innovation, challenges in technology adoption and skill development must be addressed to fully capitalize on the transformative potential of advanced MES solutions.