Unlocking the Power of CAD Software for Mechanical Designers
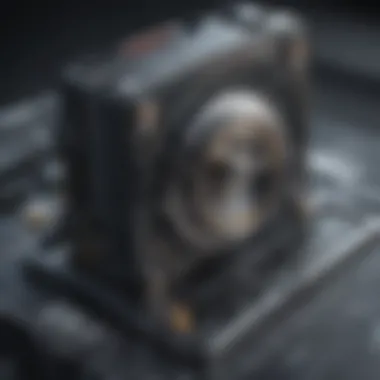
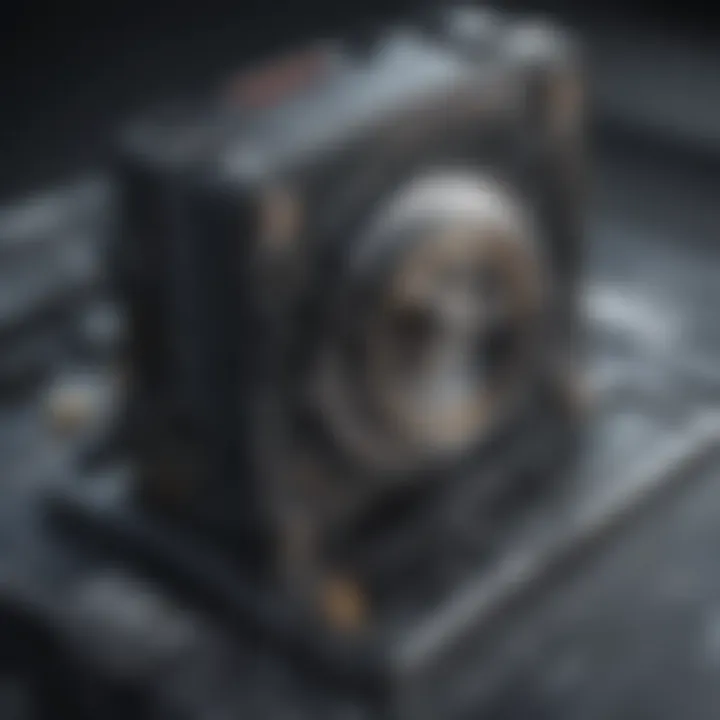
Software Overview
The realm of CAD software tailored for mechanical design is vast, encompassing a myriad of tools each with distinct features and functionalities. These tools are designed to streamline the mechanical design process, offering solutions for tasks ranging from 2D drafting to intricate 3D modeling. Understanding the core aspects of these software applications is crucial for modern engineering practices, as they play a pivotal role in transforming concepts into tangible designs.
Pros and Cons
Delving into the strengths and weaknesses of CAD software for mechanical design is essential for professionals in IT-related fields and aspiring students looking to delve into the intricacies of mechanical design. Highlighting the advantages and benefits of using these software tools will provide insights into how they can enhance the design process. Similarly, addressing the limitations and shortcomings of these tools will prepare users for potential challenges they may encounter.
Pricing and Plans
Exploring the pricing and subscription options for CAD software tailored for mechanical design is crucial for making informed decisions regarding investment in these tools. Evaluating the value for money in relation to the features offered by these software applications will aid in determining whether they align with specific requirements and budget constraints. Additionally, identifying if free trials or demo versions are available will allow users to test the software before committing to a purchase.
Expert Verdict
Concluding with final thoughts and recommendations on CAD software for mechanical design will offer readers a comprehensive assessment of the capabilities and potential of these tools. Providing insights into the target audience best suited for utilizing these software applications will guide professionals, software developers, and students towards optimizing their mechanical design process. Speculating on potential future updates and improvements to these tools will foster discussions on the evolving landscape of CAD software in the realm of mechanical design.
Introduction to CAD Software for Mechanical Design
In the vast landscape of mechanical design, CAD software stands as a paramount tool for engineers and designers. The intricate process of bringing ideas to life in the realm of mechanical engineering necessitates precision and innovation, qualities that CAD software encapsulates seamlessly. As we embark on a journey to delve into CAD software tailored specifically for mechanical design, we are met with a plethora of tools that cater to different aspects of the design process.
Understanding CAD Software
Evolution of CAD in Mechanical Design
The evolution of CAD in mechanical design has been a transformative journey, revolutionizing the way engineers conceptualize and execute their ideas. From the rudimentary beginnings of drafting to the sophisticated digital realm of 3D modeling, CAD has not only expedited the design process but also elevated the level of precision achievable in mechanical engineering. Its ability to seamlessly integrate design elements and iterate rapidly has made it a cornerstone in modern design practices.
Key Features of CAD Software
The key features of CAD software play a pivotal role in amplifying the design process for mechanical engineers. With functionalities ranging from parametric modeling to simulation and analysis, CAD software empowers engineers to visualize, optimize, and validate their designs with unparalleled accuracy and efficiency. The adaptability and robustness of these features make CAD software a indispensable asset for mechanical design projects.
Importance of CAD in Mechanical Engineering
Efficiency in Design Processes
Efficiency in design processes is a critical aspect of CAD software's contribution to mechanical engineering. By streamlining tasks such as drafting, modeling, and testing, CAD software significantly reduces the time and resources required to bring a design from concept to reality. The automated workflows and precision tools embedded in CAD software enhance productivity and enable engineers to focus on refining their designs.
Precision and Accuracy Benefits
The precision and accuracy benefits offered by CAD software are unparalleled in the realm of mechanical engineering. By enabling engineers to create intricate designs with micron-level accuracy, CAD software ensures that the final product meets the required specifications and quality standards. The ability to simulate real-world conditions and analyze critical parameters equips engineers with the tools to iterate and optimize their designs effectively.
Types of CAD Software for Mechanical Design
In this comprehensive article on CAD software for mechanical design, we delve into the significance of different types of CAD software. Understanding the diverse landscape of CAD tools is crucial for engineers and designers looking to streamline their designing processes. From 2D CAD software to integrated CADCAM solutions, the variation in tools offers specific functionalities that cater to distinct requirements within mechanical design.
2D CAD Software
Functionality and Applications
2D CAD software plays a fundamental role in the initial stages of the design process. Its functionality lies in creating precise two-dimensional drawings essential for concept visualization and drafting. This aspect of CAD software significantly contributes to laying the foundation for intricate 3D models by providing accurate geometric representations. The key characteristic of 2D CAD software is its precision in portraying technical drawings, making it a popular choice for engineers requiring schematic illustrations. One unique feature of 2D CAD software is its ability to facilitate rapid revisions and modifications, enhancing efficiency in design iterations.
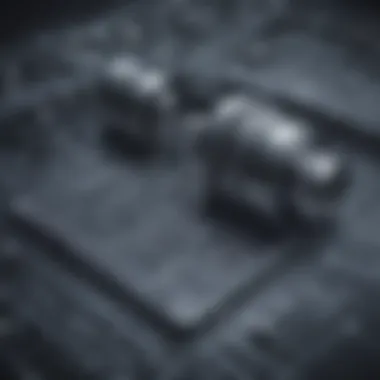
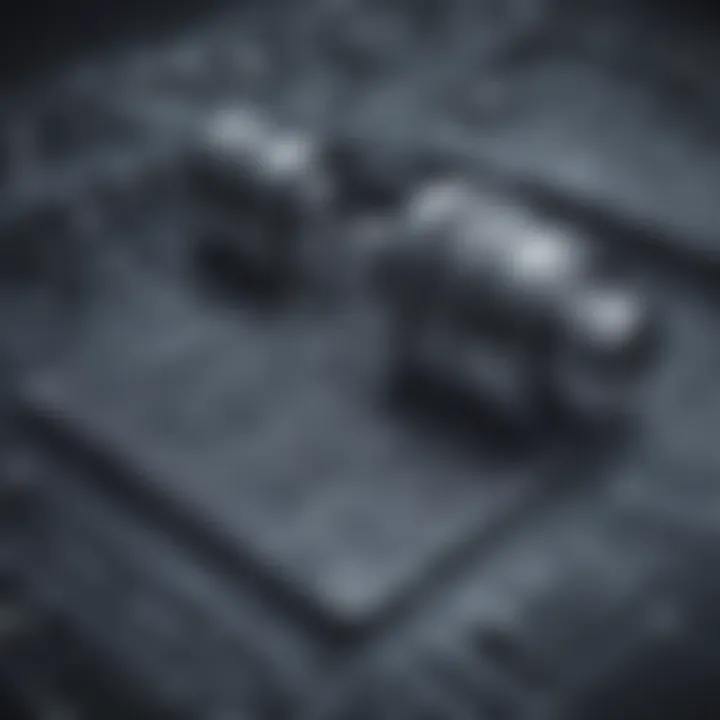
Popular 2D CAD Tools
When exploring popular 2D CAD tools, certain software stands out for their user-friendly interfaces and extensive libraries of drafting symbols. These tools not only streamline the drafting process but also ensure compatibility with other CAD software for seamless project collaboration. One noteworthy characteristic of popular 2D CAD tools is their intuitive design functionalities that simplify complex drafting tasks. However, while these tools offer extensive features, some may lack advanced 3D modeling capabilities, which could be a limitation depending on the project requirements.
3D CAD Software
Advantages of 3D Modeling
The transition from 2D to 3D modeling marks a significant advancement in modern design practices. 3D CAD software allows for the creation of realistic three-dimensional models with detailed geometry and spatial relationships. This aspect not only aids in visualizing the final product but also enables precise simulations and analyses for optimal performance. The key advantage of 3D modeling lies in its ability to represent complex designs accurately, providing a holistic view that enhances decision-making throughout the design phases.
Top 3D CAD Solutions
Among the myriad of 3D CAD solutions available, certain software stands out for their advanced features such as parametric modeling and simulation capabilities. These tools offer unmatched versatility in creating intricate designs and conducting in-depth analyses for design optimization. A key characteristic of top 3D CAD solutions is their ability to integrate seamlessly with other engineering software, facilitating a cohesive design workflow. However, the complexity of some features may require additional training to fully leverage their capabilities.
Integrated CADCAM Software
Seamless Design to Manufacturing Workflow
Integrated CADCAM software bridges the gap between design and manufacturing processes, ensuring a smooth transition from concept to production. This aspect streamlines the workflow by enabling direct communication between design and machining functionalities. The key characteristic of integrated CADCAM software is its ability to generate machine-ready codes directly from the design, reducing errors and minimizing production lead times. One unique feature of this software is its real-time feedback loop, allowing designers to optimize designs for manufacturability on the go.
Notable CADCAM Platforms
When considering notable CADCAM platforms, software known for their robust CAM functionalities consistent with dynamic design environments stand out. These platforms offer comprehensive toolpath planning and simulation capabilities, ensuring efficient manufacturing processes with minimal material wastage. A key characteristic of notable CADCAM platforms is their adaptability to diverse machining requirements, catering to a wide range of industry-specific needs. However, the sophistication of these platforms may require specialized training to maximize their full potential.
Key Features of CAD Software
CAD software plays a pivotal role in the field of mechanical design, offering a multitude of features that streamline the design process and enhance productivity. These key features are essential for creating precise and intricate mechanical designs while reducing errors and improving efficiency. Some of the notable features include parametric modeling, assembly design capabilities, simulation, and analysis tools.
Parametric Modeling
Benefits of Parametric Design
Parametric design allows engineers to create complex 3D models by defining parameters that govern the model's shape and size. This feature encourages design flexibility, as any modifications automatically update related aspects of the model, saving time and ensuring consistency in the design. Parametric modeling enhances the iterative process of design refinement, enabling engineers to explore various design options efficiently.
Examples of Parametric CAD Software
Leading CAD software such as SolidWorks and Autodesk Inventor are popular choices known for their robust parametric modeling capabilities. These tools empower engineers to create intricate models with ease and accuracy. The parametric nature of these software applications enables users to make quick design changes, assess their impact, and iterate rapidly, ultimately leading to well-refined mechanical designs.
Assembly Design Capabilities
Enhancing Mechanical Assemblies
Assembly design tools facilitate the creation of complex mechanical assemblies by allowing engineers to simulate the interaction between individual components. This feature aids in optimizing the assembly process, ensuring that all components fit together seamlessly and function as intended. By visualizing the assembly virtually, engineers can detect interferences or clashes early in the design stage, preventing costly errors in the manufacturing process.
Leading Assembly Design Tools
Software such as Siemens NX and PTC Creo provide engineers with advanced assembly design functionalities, enabling them to construct intricate assemblies with precision. These tools offer collaborative features that allow multiple team members to work on the same assembly simultaneously, promoting efficiency and coordination in design projects. The sophisticated capabilities of leading assembly design tools contribute significantly to the overall success of mechanical design projects.
Simulation and Analysis
Importance of Simulation in Mechanical Design
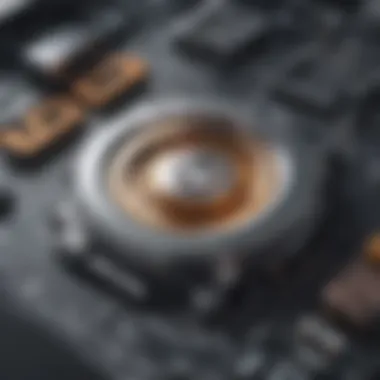
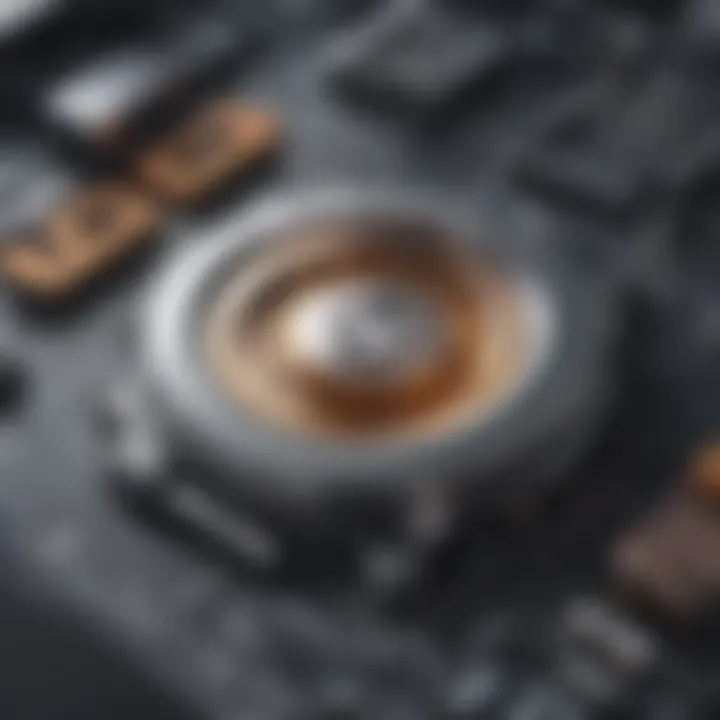
Simulation tools are indispensable for validating the performance and functionality of mechanical designs before actual production. By subjecting designs to various simulations, engineers can assess factors like stress distribution, thermal properties, and fluid dynamics, ensuring the design meets performance requirements and remains structurally sound. Simulation in mechanical design minimizes the risk of errors and enhances design optimization.
Top Simulation Features in CAD Tools
Leading CAD software offers a range of simulation features, including finite element analysis (FEA) and computational fluid dynamics (CFD), that empower engineers to delve deep into design analysis. These tools provide insights into how designs will behave under different conditions, allowing engineers to refine and improve designs iteratively. By leveraging advanced simulation features, engineers can make informed design decisions, resulting in optimized mechanical designs that meet stringent performance criteria.
Selection Criteria for CAD Software
When delving into the vast realm of CAD software for mechanical design, one must be cognizant of the critical aspect of selecting the most appropriate tool for the job. The selection criteria act as the cornerstone of aligning the features and capabilities of CAD software with the specific needs of mechanical engineering projects. By meticulously evaluating factors like functionality, scalability, and compatibility, engineers can optimize their design processes for maximum efficiency and accuracy. Understanding the nuances of selection criteria is paramount in leveraging CAD software to its full potential to meet industry demands and achieve project objectives.
Industry Specific Needs
Customization for Mechanical Engineering
In the context of mechanical design, customization plays a pivotal role in tailoring CAD software to address the unique requirements of engineering projects. The ability to customize features, templates, and workflows according to the intricacies of mechanical designs enhances productivity and precision. Engineers can configure the software to streamline design processes, improve collaboration, and ensure compliance with industry standards. Customization empowers mechanical engineers to optimize their workflow and achieve superior outcomes in complex design tasks.
Compatibility with Industry Standards
Another crucial aspect of CAD software selection is adherence to industry standards within the mechanical engineering domain. Opting for software that seamlessly integrates with industry-specific protocols and regulations ensures consistency, interoperability, and compliance throughout the design lifecycle. Compatibility with industry standards minimizes errors, enhances communication across teams, and fosters a cohesive design environment. By prioritizing compatibility, mechanical engineers can uphold quality benchmarks, streamline project delivery, and mitigate risks effectively.
Cost and Licensing Considerations
Budget-Friendly Options
When evaluating CAD software, considering budget-friendly options is essential for optimizing cost efficiency without compromising on quality. Affordable software solutions offer a favorable cost-benefit ratio, making them appealing choices for small to medium-scale engineering projects. By selecting budget-friendly CAD tools, engineers can allocate resources judiciously, maximize ROI, and explore advanced features within a constrained budget.
Subscription vs. Perpetual Licenses
The decision between subscription-based and perpetual licensing models poses a significant consideration in CAD software procurement. Subscription-based licenses provide flexibility, regular updates, and lower initial costs, ideal for short-term projects or industry novices. On the other hand, perpetual licenses offer long-term affordability, full access to software versions, and greater control over licensing terms, making them suitable for large-scale enterprises and established engineering firms.
Learning Curve and Support
Ease of Use for Beginners
Ease of use is a critical factor in CAD software selection, particularly for beginners and entry-level engineers looking to harness the software's capabilities swiftly.. Intuitive interfaces, comprehensive tutorials, and user-friendly features ensure a smooth onboarding process and accelerate proficiency development. Software ease of use fosters creativity, minimizes errors, and instills confidence in users, regardless of their expertise level.
Availability of Training Resources
Adequate training resources extend invaluable support to CAD software users, offering guidance, tutorials, and learning modules to enhance skill development and proficiency. Access to comprehensive training materials, webinars, and online forums enriches the user experience, promotes continuous learning, and facilitates skill enhancement. CAD software with ample training resources empowers users to unlock advanced features, troubleshoot issues, and maximize productivity in their design endeavors.
Advancements in CAD Technology
In this article, we delve into the critical domain of Advancements in CAD Technology within the realm of CAD software tailored for mechanical design. This exploration is pivotal as it sheds light on how technological progress plays a crucial role in streamlining mechanical design processes. By focusing on advances in CAD, engineers can harness cutting-edge tools to elevate their design efficiency and precision, leading to groundbreaking outcomes. Understanding the nuances of Advancements in CAD Technology is paramount for professionals looking to stay at the forefront of innovation and maximize their design capabilities.
Cloud-Based CAD Solutions
Benefits of Cloud Integration
Cloud Integration stands as a cornerstone in modern CAD software as it revolutionizes collaboration and accessibility. The key element of Cloud Integration is its ability to facilitate seamless sharing and real-time collaboration among team members, irrespective of their physical locations. This feature resonates well with the overarching goal of enhancing teamwork within mechanical design projects. Moreover, the flexibility and scalability offered by Cloud Integration make it a popular choice for firms seeking dynamic and efficient design solutions. However, users must be mindful of potential security risks associated with cloud-based systems and ensure data protection measures are in place to safeguard valuable intellectual property.
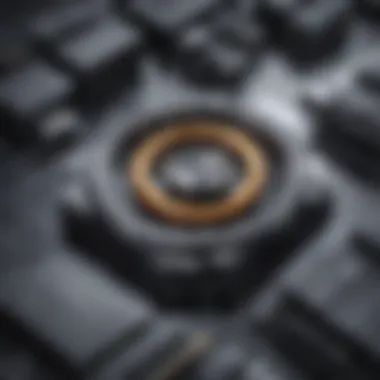
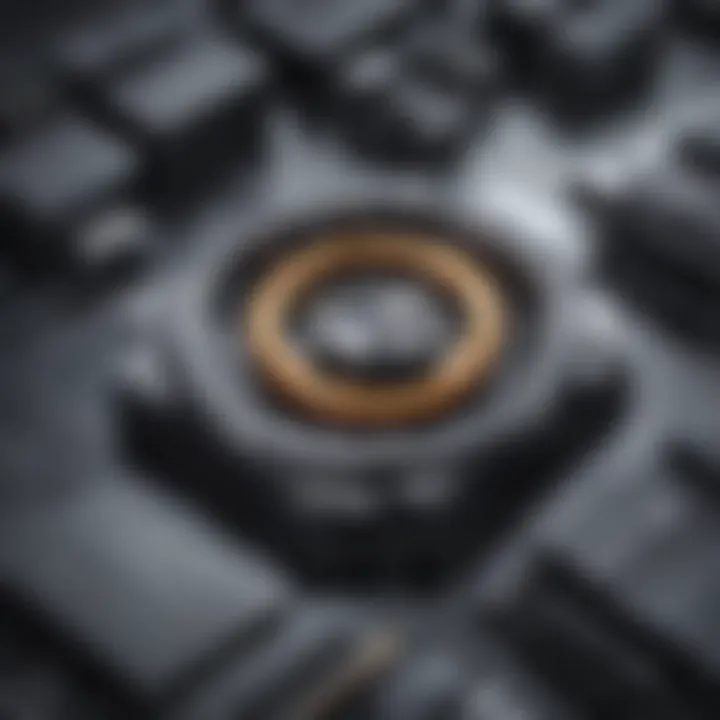
Prominent Cloud CAD Platforms
When considering CAD software options, Prominent Cloud CAD Platforms emerge as frontrunners in facilitating cutting-edge design experiences. These platforms boast the crucial characteristic of offering a wide array of tools and functionalities through cloud-based architecture, enabling users to access powerful design resources remotely. The appeal of Prominent Cloud CAD Platforms lies in their versatility and adaptability to varying project requirements. Nonetheless, users should pay heed to the potential drawbacks, such as internet dependency and limited offline functionality, which can impact design workflow in areas with unstable connectivity.
Virtual Reality in CAD
Immersive Design Environments
Immersive Design Environments represent a paradigm shift in CAD technology, immersing users in virtual realms that mimic real-world design scenarios. The key characteristic of Immersive Design Environments is their ability to provide a deeply engaging and interactive design experience, fostering creativity and innovation among designers. Such environments are a beneficial choice for this article as they enable engineers to visualize complex mechanisms in a simulated 3D space, aiding in error detection and optimization. However, the adoption of Immersive Design Environments may pose challenges related to hardware requirements and user adaptability, warranting thorough readiness assessments before integrating these tools into design workflows.
VR-Enabled CAD Tools
VR-Enabled CAD Tools redefine conventional design practices by introducing virtual reality elements into the design process. These tools offer a unique feature of enabling designers to immerse themselves in lifelike design environments, enhancing spatial perception and design visualization. The advantage of VR-Enabled CAD Tools in this article lies in their ability to streamline the prototyping phase, allowing for rapid iterations and design refinements. Nevertheless, users must be cautious of potential drawbacks like simulation accuracy and hardware compatibility issues when incorporating VR-Enabled CAD Tools into their design arsenals.
Artificial Intelligence and CAD
AI-Driven Design Automation
AI-Driven Design Automation presents a game-changing approach to mechanical design by leveraging artificial intelligence algorithms to automate repetitive design tasks. The key characteristic of AI-Driven Design Automation is its capability to accelerate design iterations, optimize solutions, and minimize manual intervention, thereby enhancing design efficiency and productivity. This transformative feature makes AI-Driven Design Automation a popular choice for this article, enabling engineers to focus on high-level design aspects rather than routine tasks. However, users must carefully validate the output generated by AI algorithms to ensure design integrity and precision.
Integration of AI in CAD Software
The Integration of AI in CAD Software heralds a new era of smart design tools that leverage machine learning and predictive analytics to enhance design decision-making processes. A key characteristic of this integration is its ability to offer predictive insights, optimize design parameters, and suggest innovative solutions based on data-driven analyses. This advantageous feature aligns well with the goals of this article, empowering engineers to explore unconventional design approaches and achieve optimal outcomes. Yet, users need to exercise caution regarding data privacy and model biases when deploying AI-integrated CAD software, emphasizing the importance of ethical AI practices and continuous model validation.
Future Trends in CAD for Mechanical Design
In the landscape of mechanical design, future trends in CAD software play a pivotal role in advancing engineering practices. As technology evolves, staying abreast of emerging trends becomes imperative for professionals in the field. The integration of innovative features and functionalities enhances design capabilities, offering unparalleled efficiency and precision. Embracing these trends enables mechanical engineers to tackle complex challenges with sophistication and ingenuity.
Generative Design
Exploring Generative Design Concepts
Generative design, within the realm of CAD software, revolutionizes the approach to creating designs by leveraging algorithms to explore numerous design possibilities based on specified parameters. This method opens up a realm of creativity and optimization not easily achievable through traditional design processes. The autonomy of generative design allows for rapid iteration and exploration of diverse solutions, fostering innovative outcomes tailored to specific objectives. Despite its computational intensity, generative design excels in producing organic, efficient designs that push the boundaries of traditional engineering methodologies.
Applications in Mechanical Engineering
Generative design finds extensive applications in mechanical engineering by enabling engineers to explore unconventional design solutions that optimize performance and efficiency. From automotive to aerospace industries, generative design facilitates the creation of lightweight, structurally optimized components that withstand stringent performance requirements. The ability of generative design to generate complex geometries that adhere to functional and manufacturing constraints showcases its adaptability and versatility in addressing various engineering challenges. Leveraging generative design in mechanical engineering not only accelerates the design process but also leads to innovative solutions that enhance product performance and durability.
Collaborative CAD Environments
Real-Time Collaboration Tools
Collaborative CAD environments introduce real-time collaboration tools that streamline communication and cooperation among team members involved in the design process. These tools facilitate instant feedback exchange, allowing for seamless integration of multiple perspectives and expertise. The interactive nature of real-time collaboration tools promotes efficiency and accuracy in design iterations, fostering a dynamic and synergistic work environment. By enabling simultaneous editing and reviewing of design components, real-time collaboration tools enhance team productivity and cohesion, ultimately leading to expedited project timelines and superior design outcomes.
Enhancing Teamwork in Design Projects
Enhancing teamwork in design projects through collaborative CAD environments cultivates a culture of collective innovation and shared responsibility among team members. By breaking down communication barriers and promoting transparency, collaborative CAD environments empower team members to contribute unique insights and expertise, fostering creativity and problem-solving skills. The iterative nature of teamwork in design projects not only enhances individual growth but also fosters a collective sense of achievement and ownership in the final design outcomes. Embracing collaborative CAD environments encourages collaboration across disciplines and departments, promoting holistic solutions that address multifaceted design challenges.
Sustainable Design Practices
Green Engineering Initiatives
Green engineering initiatives within CAD software emphasize environmentally conscious design practices that prioritize sustainability and resource efficiency. By incorporating green engineering principles into design processes, engineers can minimize environmental impact while optimizing product performance and longevity. Green engineering initiatives promote the use of renewable materials, energy-efficient designs, and waste reduction strategies, aligning engineering practices with eco-friendly objectives. The integration of green engineering initiatives not only supports environmental conservation efforts but also enhances the market competitiveness of products by appealing to environmentally conscious consumers.
Integration of Sustainability Features
The integration of sustainability features in CAD software involves incorporating tools and functionalities that enable engineers to assess and improve the environmental impact of their designs. By providing insight into energy consumption, material usage, and lifecycle analysis, sustainability features empower engineers to make informed decisions that prioritize environmental sustainability. The seamless integration of sustainability features into the design workflow promotes a holistic approach to product development that considers environmental implications at every stage. Leveraging sustainability features not only promotes responsible design practices but also fosters a culture of environmental stewardship within the engineering community.